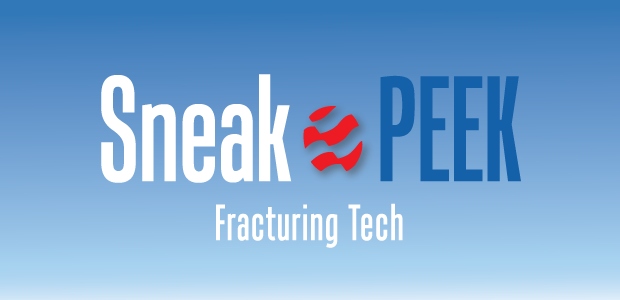
Pragmatic Ideas Simplify Fracturing
By Colter Cookson
As pressure pumpers test next-generation fleets powered by natural gas, they simultaneously are finding ways to accomplish more with legacy equipment. These efforts are confirming that streamlined processes, precise automation and tailored chemistries can enable fleets to move more fluid at a lower cost.
In addition to supporting internal and external bottom lines, service companies say their increased efficiency is helping them reach environmental performance goals and stretch capital.
“The oil field service side of the industry has gotten shrewd about capital deployment,” assesses John Gibson, chairman, chief executive officer and president of Flotek Industries Inc. “Instead of overbuilding when prices are up only to have excess capacity when they fall, companies are trying to make money for their shareholders on a full-cycle basis.”
As evidence for that thesis, Gibson cites ProFrac’s acquisition of FTSI and its agreement to acquire U.S. Well Services. “Industry thought leaders are consolidating crews into their portfolios so they can gain market share and economies of scale while holding the total fleet count at a healthy level,” he says. “They should succeed unless private equity pours into the industry to chase half-cycle economics.”
Increasingly effective completion fluid additives can deliver stronger performance at lower volumes, which Flotek reports reduces costs, simplifies logistics and minimizes environmental impacts. The company says thorough testing is key to identifying the best formulations for a particular application.
Many pressure pumpers are looking at retiring older, less fuel-efficient fleets, Gibson adds. “To shrink costs and emissions, they want to maximize their ability to use field gas and minimize the need for diesel,” he explains.
Strong environmental performance will become more important over time, Gibson argues. “With investors across the energy value chain prioritizing environmental performance, we are going to see premiums paid for more sustainable production,” he says. “As these premiums become more common, operators will work with their service providers to secure them.”
Green Chemistry
When evaluating whether a change will improve environmental performance, Gibson recommends looking at every step in the process. “Sometimes an idea that sounds green at first can turn out not to be,” he cautions. “For example, we often see friction reducers transported to site as dry products rather than emulsions. The dry products are more compact, so using them lets companies send fewer trucks to site, which intuitively reduces emissions.
“But when we look at how much energy it takes to dehydrate the friction reducer and grind it into small particles that are easy to rehydrate on site, the situation is less clear,” Gibson says. “It is difficult to tell whether the power consumption associated with those steps outweighs the extra trucks needed to move an emulsion, but if we are serious about sustainability, we need to grapple with these fundamental questions.”
It is also important to look beyond emissions, adds Flotek Chief Operating Officer Ryan Ezell. “The total environmental cost of ownership for a chemical program includes not only emissions, but also risks to water and land,” he says. “Our goal is to help in every aspect of sustainability.”
According to Gibson, minimizing those other impacts starts with seeking more benign chemistries. “Where we can, we are replacing traditional chemistries with ones that deliver the same performance but are biodegradable and nontoxic,” he says. “When that is not possible–and even when it is–we ask ourselves how we can get the same result with less chemical. If we do that, we will have fewer trucks on the road, which simplifies logistics and generally reduces emissions.”
Minimizing volumes often involves using more efficient chemicals, Gibson says. “Even with friction reducers, we are learning that we can get the same performance at a lower cost with the right chemistries,” he says. “Pound for pound, these chemistries may be more expensive than traditional ones. However, because we need less, overall costs go down considerably.”
Partnerships’ Value
Many other chemistries have more benign or efficient alternatives, Gibson comments. “We are constantly looking for replacement chemicals,” he reports.
Compelling replacements often leverage materials from beyond the oil and gas industry’s boundaries, Ezell mentions. “For example, there is a lot of food waste going into landfills. Are there ways to break down those wastes to extract the natural fats, oils and sugars, then modify those for use as oil and gas additives?” he illustrates. “What about waste from making paper? Repurposing solvents from paper mills would offer both environmental and economic gains.”
Realizing novel chemicals’ potential takes strong communication and collaboration, Ezell stresses. “When people have spent the past decade applying friction reducer at concentrations around a gallon per thousand, they will be skeptical if you tell them a more effective polymer will work with a concentration of only a quarter gallon per thousand. As a result, the well may be overtreated,” he says. “What often happens is that we send the polymer into the field only to see costs go up because too much was applied.”
In other situations, a supply chain specialist who is unfamiliar with the lab-tested superiority of a polymer may look askance at its higher unit cost, Ezell continues. “We have a much better shot at improving completion fluids’ performance when operators, pressure pumpers and chemistry providers involve the right people in the evaluation process,” he says. “Ideally, chemical selection should be guided by testing and long-term research and development. Producers that invest in research and approach the process collaboratively with an expert in chemistry such as Flotek end up with fantastic wells.”
Ezell acknowledges that many companies lack internal testing resources. “We have had companies come to us requesting friction reducers, biocides, clay control additives, corrosion inhibitors and surfactants,” he says. “When we ask whether they have tested those components together, we sometimes get ‘What do you mean?’ At that point, we ask for cuttings, core samples and produced water, bring those into our lab and run tests so we can prescribe the right mix of chemistries.”
To demonstrate the benefits of that testing, Ezell points to surfactants. “We have data from more than 14,000 wells worldwide showing that our flagship surfactants can make a marked improvement in production, but we also have seen wells for which they would be a poor fit,” he says. “When we tell customers our technology is not right for their well, we may lose some revenue on a particular pad, but because we only recommend chemistries when they are needed, the relationship is strengthened. Our business model is built on long-term partnerships, and we believe this is the best way to create value for our suppliers, customers and shareholders.”
Unlocking Efficiency
There are tremendous opportunities to improve hydraulic fracturing operations’ safety and efficiency, says Jeff Beach, vice president of technology and technical services for Universal Pressure Pumping. “One of the ways we can do that is to leverage automation to enable remote operations,” he details. “This reduces the headcount at the well site, but the big value is consistency and repeatability. An automated system can deliver above-average performance stage after stage, well after well.”
For operational safety, Beach says, most fracturing automation needs to be performed on site in the data van rather than at a remote facility. “Should the telecommunications link become disrupted, the automation and control equipment needs to be self-sufficient to spot potential operational issues and take action immediately,” he explains.
A control center in Houston may send the operating parameters through a data link to the fleet (saying, for example, that a stage requires 100 barrels a minute at 10,000 psi), at which point the well site’s automation system takes over. The system divides the work among pumps, optimizing each pump’s parameters according to the job’s requirements, Beach describes. On dual-fuel fleets, the optimization routines usually focus on maximizing natural gas substitution to minimize fuel costs and emissions, he illustrates.
Universal Pressure Pumping says it is deploying automation and novel chemistries to boost its hydraulic fracturing fleets’ efficiency and protect the environment.
The automation systems also try to limit equipment wear and tear, Beach continues. However, he says, it is sometimes worthwhile to push equipment to meet time constraints or other goals.
“Optimizing the pumps’ RPM and transmission gear takes some proprietary expertise,” he comments. “The history of the engine and how it has performed in the past, and even more specifically on the previous stage, influence the right starting point for both parameters.”
If a pump needs to be taken off line for maintenance or repairs, the automation system can determine whether it makes more sense to bring an idle pump on line or distribute the load among the remaining active pumps, Beach says. “These evaluations and decisions are being made continuously behind the scenes,” he emphasizes. “The automation system can monitor far more than a human and never gets tired, so it can intervene more frequently and consistently, which helps prevent wild swings in performance from stage to stage, well to well and pad to pad.”
Friction Reducers
Friction reducers can have a huge impact on pump efficiency, Beach reports. “As water and proppant flow through the piping and other iron on location, the friction effects compound, resulting in higher treating pressures and therefore higher horsepower requirements to get the job done,” he says. “Introducing the right friction reducer can minimize pressure needs and lessen horsepower requirements, fuel consumption and wear and tear on equipment.”
On larger jobs, optimizing friction reducers can result in eliminating one or more active pumping units, Beach says. “For a friction reducer to be as effective as possible, it needs to match the inherent chemistry of the water at the well site,” he advises. “On most locations, we are using produced water that may come from several storage sites. This diversity means water’s quality can change from day to day, hour to hour and even minute to minute.
“With that reality in mind, we are taking steps to measure water chemistry and rheology in real time,” Beach reports. “At minimum, this will let us adjust how much friction reducer we use during each job. However, the recipe for success may call for us to pivot to other friction reducers as the chemistry changes. If we do that, we should reduce horsepower requirements.”
Beach mentions that Universal has partnered with a biotech company from outside the industry to address bacteria in more environmentally friendly ways. “Traditional glut quat combination biocides stay in the water long after they are introduced,” he says. “Our partner’s technology, which is not a biocide even though it serves the same function, may let us control bacteria at surface and down hole for several months. At a predictable time, the treatment will biodegrade, leaving the water’s composition unchanged.”
Future Fleets
To reduce costs and emissions, Beach says Universal and other pressure pumping companies are eyeing investments in fleets powered entirely by natural gas. However, he predicts that Tier IV dual fuel engines with the ability to burn both natural gas and diesel will account for 70%-80% of activity, with gas-only fleets picking up the remainder.
“In many areas, getting field gas to location in the quantities natural gas-only fleets require–and processing that gas to remove contaminants–can be an undertaking. Fields with several wells and gas gathering infrastructure can manage it, but there are enough fields without that infrastructure for dual-fuel engines’ flexibility to be valuable,” he assesses.
It is often possible to fuel natural gas fleets by trucking compressed gas to site, Beach notes. “Even with CNG selling at $15 an Mcf in some areas, it still costs less than diesel, so at face value, there is a commercial benefit to using it,” he observes. “But on many pads, the logistics involved in bringing CNG to site tip the scale enough so that CNG is no longer an obvious choice.”
When natural gas is available, the cost savings and emissions reductions make it preferable, Beach emphasizes.
“Natural gas-powered fleets are evolving,” he says. “Traditional electric frac designs use a large turbine to power a 30-megawatt electricity generator. This works well, but the central turbine rarely gets to operate near 100% capacity, where it has the greatest fuel efficiency and lowest emissions. To keep equipment in its sweet spot, other fleets use a series of much smaller power generators that can be brought on line or shut off as needs change.”
The smaller generators run off reciprocating natural gas engines rather than turbines. According to Beach, emissions from these engines are lower than a turbine. However, turbines can burn a much wider Btu range of gas.
“To combine turbines’ more complete fuel combustion with the advantages of smaller equipment, some industry players are moving toward placing small turbines from the aircraft industry on trailers to drive pumps directly,” Beach relates. “This approach, called turbine direct drive, lets each turbine run at or near maximum horsepower to improve fuel efficiency and cut emissions.”
Shrinking On-Site Footprints
As they build natural-gas-powered fleets, hydraulic fracturing companies are simplifying operations and maintenance by packing more horsepower into each pump, observes Jason C. Williams, vice president and director of engineering at ShalePumps LLC. “We have developed natural-gas-powered pump trailers that can deliver 7,000 horsepower in a footprint comparable to a conventional 2,500 horsepower quintuplex trailer,” he says.
High rod load capability is a must for pumps to endure the forces created at such high horsepower, Williams describes. “Where a typical 2,500 horsepower pump may have a max rod load capacity between 200,000 and 220,000 pounds, the high-horsepower pumps can withstand 395,000 lbs,” he says. “That capability comes from thicker, heavier materials.”
While high-horsepower pumps can be powered electrically, Williams predicts that most will be driven mechanically. “Using aeroderivative natural gas-powered turbines to drive the pumps eliminates the need for an electric motor or variable frequency drives,” he explains. “Instead, the turbines on each trailer transfer power to the pump through a multispeed transmission.”
New hydraulic fracturing fleets often use higher-horsepower pumps to streamline maintenance, shrink site footprints and ease operations, ShalePumps LLC observes. To minimize fuel costs and emissions, many of these pumps are powered by aeroderivative turbines that run on natural gas.
The simpler design translates into lower costs, Williams reports. “We can field a fleet of 7,000 horsepower units powered by mechanical drives for almost the same price as a fleet of new conventional Tier IV 2,500 horsepower units,” he clarifies. “The high-horsepower, direct-drive fleets can shave as much as $10 million or $15 million off the cost to build a natural gas-powered fleet.”
Horsepower density is key, Williams says. “With 5,000 horsepower pumps driven by turbines, the cost for each horsepower may be 15%-20% higher than for a conventional 2,500 horsepower Tier IV fleet,” he contrasts. “As the pumps’ horsepower goes up, the cost per horsepower falls into line with that of conventional fleets. These savings are why we see high-horsepower pumps connected to aeroderivative turbines as the most likely path forward.”
Turbines’ Virtues
According to Williams, direct-drive fleets’ virtues have been validated independently by a study presented at the 2021 DUG East conference. During the study, the emissions testing firm Air Hygiene International Inc. and West Virginia University’s Center for Alternative Fuels, Engines and Emissions quantified the emissions associated with several fleet types. “Ultimately, the study concluded that direct-drive turbines were the most efficient way to power fleets from both an emission and cost perspective,” Williams summarizes.
The aeroderivative turbines are extremely reliable, he assures. “Conservative estimates put their lives between 60,000 and 70,000 hours, about three times the life expectancy of a typical piston-drive diesel engine,” he reports. “The turbines are new to the oil and gas industry, so no one has run them that long yet. However, some of the aircraft engines on which they are based have logged more than 100,000 hours.”
Like all mechanical drives, the turbines’ output will vary based on environmental conditions, Williams says. For turbines, one of the biggest factors is the amount of oxygen in the intake air, which declines at higher elevations and temperatures. “During summer in West Texas, a hot area that is well above sea level, the twin turbines on each trailer may top out at 7,200 or 7,300 horsepower,” he calculates. “During winter, when the air is cold and dense, the turbines’ output can jump to 8,600 or 8,800 horsepower, which should allow pumps to achieve higher rates.”
To limit fuel consumption and emissions, the aeroderivative turbines can be turned off as needed, Williams says. “There is no need to conduct a lock out and tag out inspection when they are shut off or turned on. In fact, the turbine can turn back on 20 seconds after shutdown and hit full power within a minute.”
For other great articles about exploration, drilling, completions and production, subscribe to The American Oil & Gas Reporter and bookmark www.aogr.com.