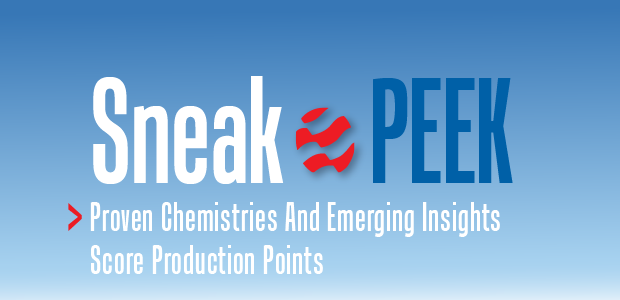
Production Optimization
Proven Chemistries And Emerging Insights Score Production Points
By Colter Cookson
To thrive in a tough environment, oil and gas producers often draw on the same characteristics that allow professional basketball players to succeed on the court. They put in the time to master essential skills, have the situational awareness and agility to adapt quickly to unusual events, and work with others to unlock their assets’ full potential.
And like the general managers who must decide whether to pay a star’s salary or develop promising young talent, producers must always consider economics. To meet the world’s continuing need for oil and natural gas while maintaining strong balance sheets, they are looking for ways to drill and complete new wells at lower costs while increasing production from their legacy assets.
“Operators are asking us to help them do as much or more with less,” summarizes Wayne Cutrer, chief executive officer of Downhole Chemical Solutions. “They want us to build completion fluids that can deliver the same or better performance at a lower cost.”
Because they are highly concentrated and less costly to transport than liquids, dry friction reducers shrink the chemical costs and environmental footprint associated with hydraulic fracturing, Downhole Chemical Solutions says. These savings are enabled by specialized equipment that disperses the dry FR powders into completion fluids on site.
Optimizing friction reducers is key to achieving that goal, Cutrer says, explaining that they account for 40%-70% of the chemical cost associated with slickwater completion fluids. He argues that the best way to minimize that cost is to replace liquid friction reducers with dry equivalents.
“Liquid FRs only contain 20%-30% of the active polymer that makes them effective,” he says. “The remaining 70% or 80% of their volume is a mix of oil, water and surfactants designed to carry that polymer from the plant to the wellbore. This carrier fluid serves no function down hole, but it inflates the cost associated with trucking or railing the FR to the site.
“With a dry FR, we can ship 100% active polymer to the well in 45,000-pound pneumatic trailers, then use specialized equipment on site to add it to the completion fluid.” Cutrer contrasts. “Between eliminating carrier fluid costs and reducing shipping requirements, this can shave 10%-25% off completion chemical costs.”
Despite these savings, Cutrer estimates that only one in five completions use dry FRs. “They are not more prevalent because handling and administering them can be complex. Dry FRs need to be transported to the site without being exposed to moisture, then dispersed into the completion fluid quickly,” he says.
To perform those tasks, DCS has designed equipment in house and developed and patented a more reliable method of introducing the powder into the completion fluid, Cutrer relates. In late February, he said the company had 15 dry FR units in the field, with three more coming in the next few months.
“Since we commercialized our first unit in January 2019, we have successfully treated more than 26,000 stages and pumped 19 million pounds of dry FR powder,” he reports. “Once operators try dry FRs, they generally adopt them on all their spreads. We are up to four clients with multiple units and will soon have a fifth, a sign the FRs provide significant cost reductions.”
Environmental Benefits
According to Cutrer, cost is not the only reason to switch to dry friction reducers. “It makes a massive impact on the completion’s carbon footprint,” he clarifies. “That is partly because dry FRs require fewer trucks to reach the site, but the main component is the amount of carbon used in liquid friction reducers.”
Most of that carbon comes from the carrier fluid’s mineral oil, which Cutrer says accounts for about a third of liquid FR’s volume. “Mineral oil is a refined oil with a high carbon content,” he notes. “For a completion that needs 5,000-15,000 gallons of liquid FR, eliminating the oil can keep thousands of pounds of carbon from being consumed unnecessarily.”
Dry FRs also improve safety, Cutrer adds. “Each load of dry FR can do as much as three or four loads of liquid FR, so we are greatly reducing windshield time,” he explains. “There also is less chance of spills. In fact, we do not handle the dry FR on location at all. The trailers are loaded and offloaded in a controlled environment at our facilities, virtually eliminating the risk of a spill on site.”
Optimizing ESPs
By using condition-based maintenance software to monitor electric submersible pumps for early signs of failure, operators can increase their uptime significantly, says Steve Roemerman, chairman and CEO of Lone Star Analysis.
“The degree to which monitoring extends mean time between failure varies widely, but we often see several months’ difference, with some pumps lasting half a year longer,” he details. “In some cases, those extra months come from spotting and fixing a problem down hole, such as a burned-out controller. In other cases, they result from changing pump operation.”
Lone Star Analysis’ software monitors electric submersible pumps and associated equipment to help producers maximize uptime and performance. The company says the software detects many issues weeks or months in advance.
One way the software helps production engineers is by optimizing pump speed, Roemerman notes. “If the pump is running harder than it needs to, it can heat up and burn through component life. We often can keep the pump down hole longer and get more production by slowing it so it has time to cool.”
When the software detects a sign of failure, Roemerman says it will flag the issue. “We try to give operators at least a couple months’ warning so they can order a replacement or schedule a repair and avoid hot shot fees,” he relates. “Such long lead times are not always possible, but we almost always manage to give at least a couple weeks’ notice.”
Once it identifies an issue, Roemerman says the software will recommend several solutions. For example, it may suggest changing the pump’s duty cycle or operating conditions to lengthen its run life. The software will estimate these changes’ impact on production so the operator can make an informed decision about whether to implement them, Roemerman mentions. “For an especially productive well, it may be worthwhile to run the pump at full tilt and schedule a repair rather than trying to preserve it,” he explains.
Transparent Algorithms
Roemerman describes Lone Star Analysis’ software as transparent. “If a production engineer wants to understand why the software thinks a problem is coming, they can pull up a visual representation of the pump that shows the pressures, temperatures and other data from various stages,” he assures. “Usually, they quickly see what is going on.”
In addition to drawing on readings from actual sensors, the software estimates measurements with “virtual sensors” developed by applying physics and machine learning algorithms to analogous data. These virtual sensors allow the software to make more informed decisions than it could if it had to rely solely on the downhole data, Roemerman says.
“ESPs send less data to surface than an old dial-up modem, so machine learning algorithms for optimizing them cannot rely on brute force approaches that require vast datasets,” Roemerman observes. “Instead, we tell the algorithms everything we already know, such as general principals about the way electric motors and pumps work, as well as the characteristics of the on-site equipment and the materials it is made from.
“The goal is to use machine learning only when it will help us discover something unknown, such as what is happening down hole at that specific site,” he outlines. “Because we need so little data to train our algorithms, we often start predicting failures within an hour of our software going live.”
Assuming the operator already has SCADA systems on site, Roemerman says deploying Lone Star’s software will take a week or two at most. If the client uses remote monitoring platforms from one of the company’s partners, such as ABB, deployment can be simple as checking a box and waiting 24 hours.
“We use a software as a service model where we charge a fee for each pump monitored,” Roemerman notes. “Usually, the service will pay for itself within a month.”
Post-Production Treatment
While managing logistics for Gasfrac, a company that fractured wells with liquefied petroleum gas (LPG), Tadd Wallace became so fascinated with LPG’s properties that he began pursuing a chemistry degree to deepen his understanding of them.
“When my Organic Chemistry II professor wrote an equation showing how to turn water and propane into one fluid, I smiled, shook his hand and told him I was going to start a new company,” he recalls. “I had realized we could use LPG to remove the water left behind by fracs, which is one of the biggest drivers of unconventional wells’ rapid production declines.”
According to Wallace, almost all the water injected during a frac stays below ground. Engineers can estimate the volume by monitoring the produced water’s salinity, which goes up as the well shifts from returning frac fluid to delivering reservoir water.
“There is a clear link between how much frac water remains in the formation and how quickly a well declines,” Wallace reports. “One of the big issues is that all shales contain clays, which have the ability to absorb 100% of their molecular weight in water. In the process, they swell and plug the formation. By using LPG to break that water off the clay molecules, we should be able to increase permeability and reverse the production decline.”
To implement that process, Wallace launched Universal Chemical Solutions and partnered with STEP Energy Services, a coiled tubing, hydraulic fracturing and wireline company that acquired Gasfrac’s equipment and intellectual property in 2015. Mike Burvill, STEP’s vice president of business development and innovation, expresses excitement about LPG’s ability to revive wells that would otherwise enter terminal decline.
“Based on reservoir engineering and modeling, we can significantly increase many wells’ production,” he reports. “The process works in part because LPG is miscible in oil even at low pressures. As it spreads down hole, it will mix with the oil, swelling it and causing it to move toward the wellbore.”
Injecting liquefied petroleum gas augmented by specialized chemistry into declining wells can increase production significantly, STEP Energy Services and Universal Chemical Solutions say. The production increase comes in part from LPG’s ability to improve permeability by deswelling water-laden clays.
Wallace points out that the industry has long used miscible gases such as carbon dioxide to enhance recovery through huff-and-puff treatments. “The beautiful thing about this technology is that the science works,” he says. “The gas may be different, but the core concept is something even a first-year engineer will understand and appreciate.”
Although it requires specialized equipment, injecting LPG can be quite affordable, Wallace assures. “The average pump time will be between three and 10 hours, which means we can do the entire job during daylight. The total cost is low enough that we are expecting each treatment to pay for itself in 30-90 days.”
The LPG poses no risk of formation damage, Wallace adds, noting that it is one of the components the wells produce.
Potential Candidates
Burvill says LPG treatments are ideal for liquids-rich, hydrocarbon-bearing reservoirs, including tight shale or sandstones with low permeability.
“We are targeting the Delaware Basin, Eagle Ford Shale, Denver-Julesburg Basin and Bakken,” he reports. “Before each job, we will evaluate the well’s geology and initial completion to ensure the economics make sense.”
“With the Biden administration stopping fracturing on federal lands, we are getting a lot of interest from operators with assets there,” Wallace comments. “The treatments only require a small spread and do not involve fracturing, so we may be able to boost those operators’ production when traditional solutions cannot.”
Wallace adds that the treatments require no water, which could make them especially appealing in arid regions such as West Texas and New Mexico.
The Right Water
By using the right water for the formation during drilling, hydraulic fracturing and enhanced oil recovery operations, producers may be able to increase the extractable original oil in place as much as 15%, says Salem Thyne, CEO of ESal.
Using water with the right salinity to bring a formation toward neutral wettability can greatly increase production, ESal reports. The company says such water often can be acquired at a low cost, enabling it to slash wells’ breakeven prices and extend their lives.
“Water with the right salinity can alter the formation’s wettability, which governs whether it attracts oil or water,” he explains. “We want wettability to be neutral so that both oil and water flow through the pores and reach the wellbore.”
Thyne acknowledges that seeking neutral wettability clashes with conventional wisdom, which prizes water wettability. “The theory goes that a water-wet formation will keep some water from reaching the wellbore while allowing oil to flow through. In truth, the water restricts pore spaces and traps oil.”
Empirical evidence supports that claim, he maintains. “We have looked at 200 case studies involving waterfloods, and the best production always came at neutral wettability, while the worst showed up when a formation was extremely oil or water wet.
“We discovered this through a happy accident,” Thyne relates. “While my father, Geoff Thyne, was working at the Enhanced Oil Recovery Institute, he did a low-salinity waterflood that the models and equations suggested should be profitable. Instead, it was an absolute failure. That bothered my dad enough that he left the institute to figure out what we were not seeing.”
In his quest to discover why low-salinity waterfloods work well in some areas but not others, Geoff Thyne and his colleagues studied how water’s salinity influences a formation’s wettability. “We realized that salinity’s effect differs from formation to formation,” Salem Thyne says. “In some areas, low-salinity water will help the formation reach neutral wettability, but in others, salty water is what the formation needs.”
Variations in rock type, water and oil chemistry, and temperature all influence how water will affect wettability, Thyne explains. After looking at more than 200 reservoirs, ESal has developed quick tests for determining what sort of water will help a well or field achieve neutral wettability, Thyne reports. “Usually, the screening tests take about two weeks, while the full tests take six,” he details.
“In an old conventional well, injecting the right water should bump up production and flatten the decline curve for a few years, then put the well back on its old curve. By that point, the well should be on track to get 10% or 15% more of the OOIP.
“It is harder to predict or measure how much using wettability-optimizing water to drill and complete unconventional wells will improve production, but we think we will be able to get the average estimated ultimate recovery from 8% of the OOIP to 15%,” Thyne continues.
Sourcing better water can be cheap, he says. “Sometimes the operator is producing water with the right salinity from other benches or can buy it from someone who considers it a waste stream. In other areas, they may need to drill a water well or treat their produced water,” he details. “We work with our clients to help them find the most affordable water source.”
Thyne stresses that ESal only accepts projects where it believes optimizing water will deliver incremental production at a cost of $4 a barrel or less. “For smaller companies with conventional wells, we often do the upfront work on our dime in exchange for $1 from every incremental barrel,” he mentions. “Our goal is to prove the technology, not to make money off failed projects.”
To start ESal, Thyne says he left a 23-year career focusing on uranium enrichment in the nuclear industry. “I am really excited about the opportunity optimizing water presents,” he comments. “On average, we are reducing the breakeven prices for our clients $8-$12 a barrel. In carbonate formations, we think we can add 10-15 years of life to the stripper wells on which many small operators depend for their livelihoods.”
For other great articles about exploration, drilling, completions and production, subscribe to The American Oil & Gas Reporter and bookmark www.aogr.com.