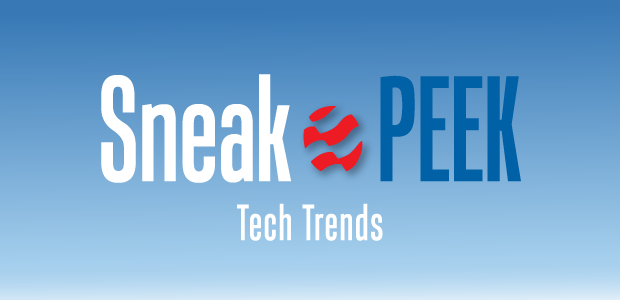
Smart Inventions Increase Production
By Colter Cookson
Existing well sites play a crucial role in the oil and gas industry’s quest to reduce methane emissions. In some cases, these sites will need to be upgraded to comply with the U.S. Environmental Protection Agency’s Quad Ob and Quad Oc rules, as well as other regulations. Recognizing that these upgrades can be prohibitively expensive, several innovators have begun developing alternatives that mitigate emissions at a more attractive price or combine emissions reductions with production increases.
Other advances are helping companies increase production from proven artificial lift techniques by making it easier to implement complex optimizations. To accelerate that progress, Liberty Lift says it has commercialized a cloud-based pump-off controller that has access to boundless processing power and the ability to constantly improve by adding new features.
For Russell Messer, director of automation and optimization at Liberty Lift, one of the most exciting recent features gives production engineers an easy way to distinguish between pump-off conditions and gas interference. Pump-off controllers monitor fillage to determine when liquid is no longer near the pump and it can be shut off, Messer notes. Unfortunately, gas interference can cause fillage to drop below a given set point even when liquid is present and pumping should continue.
By showing rod pumps’ plunger velocity on downhole pump cards, Liberty Lift’s cloud-based pump-off controller gives production engineers a quick way to tell whether low fillage values indicate a pump is empty or merely reflect gas interference. In the latter case, which tends to yield slower, more gradual plunger velocity declines, the engineer may be able to increase pump speed and production without putting equipment at risk.
This can put production engineers in a bind, Messer says. If they assume gas inference is causing the pump to stop, they can change the set point and get more production. But if they are wrong and the pump is as empty as the fillage value indicates, they will expose the rod string to extra wear and tear without increasing revenue.
Periodically, production engineers can determine the ideal set points by modeling the rod string design with the current liquid level above the pump and other recent data, Messer says. He indicates the liquid level is important partly because liquids create buoyancy, which can minimize the load on the gearbox, structure and rod string.
“When the liquid level is high or the potential for rod buckling is low, the rod string design software may give the production engineer the confidence to speed up pumping without worrying about compromising the equipment,” he says. “The problem is that even in a best-case scenario, most companies only measure the fluid level in a rod pump well every quarter or every six months. And when engineers do have a recent fluid level, modeling and optimizing the well can still take a couple hours.”
Those optimizations sometimes increase daily production by 20 barrels or 200, but spending time on them can be hard to justify for production engineers who also oversee new wells that produce thousands of barrels a day, Messer observes. “If we want production engineers to optimize rod pumps, we need a way to make opportunities for improvement jump off the page,” he reflects. “In other words, it needs to be obvious that the engineer has room to play by pumping more aggressively, or that they need to pull back to protect equipment.”
After considerable experimentation and testing, Liberty Lift realized the best way to achieve that goal was to overlay plunger velocity on the pump card, Messer relates. “When we started looking at plunger velocity, it was a huge aha moment,” he says. “Making plunger velocity more visible is one of the most exciting improvements I’ve had a chance to be a part of during my 13-year career.
“In a well that is pumped off, the plunger should accelerate during the downstroke, slam to a stop when the traveling valve reaches the fluid and opens, and resume moving. When the plunger stops, the pumpjack keeps going. That forces the rod string to buckle, which production engineers want to avoid,” Messer describes.
“But if the well only has gas interference, the plunger will slow down gradually rather than suddenly as it comes into contact with the liquid,” he contrasts. “In some cases, the plunger velocity may not slow at all. Either way, the more gradual change in plunger velocity is a strong sign the pump can be run more aggressively.”
On one well in the Austin Chalk that used fiberglass sucker rods and had a seat nipple depth around 7,500 feet, the plunger velocity barely slowed during the downstroke despite severe gas interference. Based on that information, Messer says the operator increased the strokes per minute from 11.1 to 12.5, which boosted production from 550 barrels a day to around 700.
“If we had looked at the well without considering plunger velocity, none of us would have felt comfortable increasing the speed,” Messer says. “When production engineers start seeing plunger velocity on stroke after stroke, they discover that many wells behave in unexpected ways. In some cases, they can pump more and increase production. In other cases, they need to pull back.”
The Key Enabler
While plunger velocity makes it possible to spot wells with potential for optimization quickly, that information is only useful at scale because Liberty’s newest pump off controller makes it available through the cloud, Messer says. “The controller is effectively a cell phone in the oil field,” he comments. “It was hard to develop, but we knew we had to create it because we could not address the limitations of traditional pump-off controllers without more processing power than we could put in the field.
“With the cloud, we have unlimited processing power,” he enthuses. “We are only beginning to see what we can do with that freedom.”
Messer acknowledges that some operators initially express concern about sending data to the cloud. He indicates that Liberty is adopting SOC 2, a data security framework created by The American Institute of Certified Public Accountants. “As part of that, we are working with a third-party cybersecurity company that periodically tries to break into our system to identify weaknesses, then shares them with us so they can be fixed,” he mentions.
When Liberty develops new features, it can update existing controllers’ firmware over the air, Messer notes. “On average, we are releasing an update every three months,” he reports. “Most of the updates have 15-20 new features, and we have an open roadmap of features we would like to add that currently has more than 360 entries. The cloud is allowing us to keep pushing the bounds of what’s possible.”
As a case in point, Messer cites a feature added in December that gives operators more precise control over pump speeds. “In the past, pump-off controllers would divide the pump stroke into four zones, meaning that speed could be changed four times: twice on the upstroke and twice on the downstroke,” he relates. “With the new feature, we are expanding that to 12 zones: six on the upstroke and six on the downstroke.”
Messer predicts the extra zones will have three benefits. The first relates to long-stroke pumping units, where zone control can be essential to protecting equipment. “With four zones, operators usually keep the speed at full for most of the stroke, slow down to 80% toward the top to keep from putting too much force on the load cell and the sprocket at the top of the pumping unit, accelerate to 90% as the downstroke begins, and return to 100% during the downstroke,” he outlines. “In effect, they are making the turn at the top slow and easy, then picking up speed in the straightaways.
“With 12 zones, we may be able to maintain high speeds for longer periods without putting the long-stroke pumping unit at risk,” Messer says. “In a four-zone setup, the speed is constrained by the acceleration limits that the drive imposes to protect itself. By using some of the extra zones to stair-step toward the target speed, we can stay within those limits but reach the maximum speed faster.”
The extra zone’s other potential benefits apply to conventional pumping units, where traditional zone control rarely gets used. One goal is to reduce peak loads on equipment, which may allow operators to use smaller, less expensive drives. To shrink the peak loads, the controller would slow the rod string at the point in the stroke where loads tend to be high, then make up for that slowdown by accelerating elsewhere.
For wells with gas interference, Liberty is investigating whether it’s possible to increase the effectiveness of the downhole gas separator by slowing the downstroke. To maintain the same overall speed, Messer says the controller would accelerate the upstroke.
Messer emphasizes that the more precise speed control is a new feature and that its benefits remain unproven. “As with so many ideas, we cannot pencil everything out ahead of time,” he says. “To see how big the benefits will be, we had to put the feature in and start working with operators to experiment. We do not have data yet, but we think the extra zones will let operators speed up pumps, reduce capital costs and improve gas separation.”
Addressing Quad O
When NexGen Chemical Technologies, an inventor of hydrogen sulfide scavengers, sold in May of 2023, Dallas Watson planned to spend some time tinkering with various ideas. That tinkering took on new urgency when he started getting calls from friends. “They kept telling me, ‘On many sites, we cannot afford to comply with Quad Ob using existing solutions. Can you think outside the box and develop something that is more economical and does not require an outside source of electricity?’” he recalls.
One of the biggest issues is that Quad Ob prohibits pneumatic control devices from venting gas. It’s possible to avoid such venting by switching to zero-bleed or electric valves, but Watson cautions that such conversions can be prohibitively expensive in many applications. Instead, most operators try to stick with pneumatic valves but operate them using compressed air. This approach can be more economical, but like electric valves, traditional air compressors need reliable power to run.
At first, low-cost solar panels seemed like the ideal solution, Watson relates. However, operators quickly discovered that the panels struggled to deliver sufficient power during winter, especially in the all-too-common situation in which someone stole the batteries. The batteries that do remain in place will eventually lose capacity and end up in a landfill, Watson adds. He acknowledges that some higher-end solar panels work well, but they come with a commiserate cost and footprint.
To find a new path, Watson says he began experimenting with ways to create air using energy that already exists on site. “It’s always fascinated me how much energy exists behind pipe but goes unused,” he says. “I decided to capture some of the energy that exists in the form of pressure differentials to compress air on sites without electricity.
A compressor from Capture Energy generates air for operating pneumatic valves by harnessing energy that already exists on many sites in the form of pressure differentials. Since the compressor does not need an external electricity source, Capture Energy says it offers a cost-effective way to comply with the U.S. Environmental Protection Agency’s Quad Ob regulations.
“Capture Energy’s air compressor works by using high-pressure gas to operate a piston that is connected to a pneumatic air piston,” Watson describes. “The high-pressure gas enters the cylinder and expands, oscillating a piston up or down and causing the pneumatic air piston to compress air. This air goes into an ASME-certified tank until it’s needed, while the depressurized gas gets sent back to process for resale.”
Watson emphasizes that this process converts energy from gas into air through pressure, not combustion. It does not consume any of the gas, meaning all of it can be sold.
In addition to reducing greenhouse gas emissions, selling the methane that pneumatic valves previously vented can recoup the cost of the compressor in a reasonable time frame, Watson reports. “On a well-maintained site with few leaks, the compressor pays for itself in a couple years,” he clarifies. “On sites with more leaks, the payback will be faster.”
According to Watson, the compressor’s capital efficiency comes in part from its easy deployment. “The compressor installs quickly,” he says. “It only has three lines: one that brings high-pressure gas into the compressor to operate the pistons, one that discharges the air into the vessel, and a third that exhausts the gas back to the pipeline. All the technician needs to do is plug in these lines.”
The affordability extends to operating expenses, Watson continues. “The compressor uses high-quality cylinders and stainless-steel valves that will still work well when the company owner’s grandkids are ready to take over,” he says. “Some seals will need to be replaced periodically, but they are cost-effective. Even if the entire compressor needs to be rebuilt, a trained technician can do that in minimal time using general hand tools.”
To operate, the compressor does require a meaningful pressure differential, Watson notes. While the minimum varies from site to site, he says 100 psi is a reasonable rule of thumb.
“Almost all the compressors we sell are installed on gas compressors, because those always have a high-pressure discharge that we can borrow energy from before putting the gas back,” he reports. “If a site only has 30-40 pounds of differential pressure on location going from a secondary or primary separator to sales, or if it contains marginal wells that need to keep the separator pressure as close to the line pressure as possible to maintain production, the compressor will not be a good fit.”
But there are many sites where the compressor offers an unusually economic solution, Watson says. Rather than trying to serve those sites directly, which would require investments in warehouses, sales teams and technicians, he says Capture prefers to work through distributors who already have infrastructure and people. This frees the company to focus on developing technology.
“We have been refining our manufacturing process and building an inventory for months,” he adds. “When a company orders a compressor package, we will have one ready to go.”
Plunger Control Valve
In the long run, Watson says Capture Energy would like to harness the energy on well sites for other purposes and potentially return some of it to the grid. But for now, the company is focusing on helping operators stay ahead of ever-tighter regulations.
“The interest in our compressor that we see today is only the tip of the iceberg compared to what will come when Quad Oc goes into effect in 2028,” he predicts. “At that point, thousands of wells that are on plunger lift will no longer be grandfathered in and will have to find a way to keep their plunger control valves from venting. Many of these wells only produce 30 Mcf a day and cannot afford to convert to electric valves.”
In anticipation of that need, Watson says Capture Energy has developed a retrofit kit that takes high-pressure gas from the casing and uses that gas to operate the existing control valves. However, instead of allowing the gas to vent, it redirects the gas back into the production line. “To retrofit this system, a technician takes the top off an existing valve and puts our system in,” he says. “The installation only takes about 20 minutes, and the equipment is built to last.”
The company is providing a similar solution for compressor dump valves. “This eco-friendly valve controller operates by taking high-pressure gas from the compressor discharge, using the pressure to operate the scrubber dump valve and then returning the gas to the low-pressure side of the compressor,” Watson outlines. “It does not require instrument air, and the tiny amount of electricity it needs comes from an existing internal battery that is already on the compressor skid.”
Pneumatic Pump
With Quad Oc on the horizon and some states considering even stricter rules, many stripper wells that vent methane from the casing could soon be slated for plugging and abandonment, says Gary Sommese, the founder of Air Lift Technology LLC. He points out that such venting occurs for technical reasons.
“These wells have low-pressure formations, so if the operator tried to hold the gas in the annulus rather than venting, pressure would build up downhole and inhibit any fluid from entering the wellbore,” Sommese explains. “To keep the wells on line as regulations tighten, operators need a way to reduce the bottomhole pressure while capturing the methane.”
A self-optimizing pump developed by Air Lift Technology LLC can increase marginal wells’ production while capturing methane that would normally vent to atmosphere. According to the company, the pump uses corrosion-resistant materials and has only one moving part downhole, enabling it to operate reliably even in harsh environments.
Sommese says Air Lift Technology has a solution in the form of a novel artificial lift technique that uses pneumatic energy to transport production to the surface through a series of pumps. Each pump contains a float that rises as its chamber fills. Eventually, this float activates a valve, allowing the pneumatic energy—either compressed air or gas—to enter the pump and displace the liquid into the production line, which carries the fluid up to the next pump (or in the case of the topmost pump, to the surface), Sommese describes.
With the fluid displaced, the float drops, allowing the air or gas to be exhausted from the pump and returned to the surface. Air is used as the pneumatic energy source if a well has no gas production. When gas is available, Air Lift’s system can be paired with a compressor developed by Kapture Compression LLC that captures the gas and recirculates some of it to operate the pumps, Sommese says. Natural gas that is vented from the well at the surface is therefore captured and is no longer vented to the atmosphere, he says.
“One of the advantages of the system is that it self-regulates,” he comments. “There is no need to guess how often the system needs to pump, thus eliminating the human error factor associated with timeclocks. As soon as the fluid flows into the pump and its chamber is full, the pump will clear itself out and go back into standby mode until the chamber refills.”
For an operator in Osage County, Ok., that self-regulation helped increase production by about a third during a year-long test involving 32 wells, Sommese reports. “During that test, we kept about 1 psi on the formation to mirror the pressure when the well was produced via rod lift,” Sommese recalls. “We are currently using the same surface compressor to pull a vacuum on the well at the suggestion of the University of Tulsa, which is working with us to optimize the technology. The extra suction has increased the production gain from 30% to about 50%.”
Some of the extra production comes from the system’s ability to capture gas that previously escaped through the casing or through other equipment, such as the stuffing boxes on a sucker rod pump well, says Don Aldridge, Air Lift’s marketing and technology director. “On some sites, we have had a chance to use optical gas imaging to look for methane before and after installing the system,” he says. “The difference is striking. Once our pneumatic pump is in place, there are no leaks whatsoever.”
Carbon Credits
Because of the emissions reductions, installing Air Lift’s pneumatic system alongside Kapture Compression’s compressor system can generate carbon credits, Aldridge says. “There has been some talk of plugging wells for credits,” he reports. “With our technology, operators should be able to earn those credits while extending the life of the well.”
The credits vary widely in value, but Aldridge says they should remain available regardless of political shifts in the United States. “Europe has committed to net zero, and it will need a way to accomplish that. With the Russian gas situation, the German government has had to use coal, then offset the associated emissions,” he says. “At the same time, Colorado and New Mexico have enacted regulations more stringent than the EPA while California has established a mandatory carbon market. Additionally, the SEC is requiring publicly traded companies who made net zero pledges to act. If they do not, they could face lawsuits from shareholders.”
Aldrige points out that the companies targeting net zero include household names, such as Microsoft, Google, Amazon, UPS, Merrill Lynch and J.P. Morgan. “The Microsofts and Googles of the world recognize the incredible amount of energy that AI is going to need and have pledged to the market to be net zero,” he comments.
According to Aldridge, building carbon credits usually costs less when the greenhouse gas is used rather than merely sequestered. He says Air Lift’s system can help operators leverage more of their methane by helping aggregate production. “Our systems have enough energy that they can often transport oil and gas from a well without a sales line to a central location for separation,” he reports.
The company is exploring alternative uses for stranded gas, such as generating power for AI or bitcoin mining. “A couple Mcf a day from a single well has limited value, but if we get 30, 50 or 100 Mcf into one location by drawing from several wells, we have several potential ways to leverage it,” Sommese envisions.
“We are also working with the University of Tulsa to see if we can compress stranded gas, which is coming into the system around 125 psi, up to several thousand pounds so we can store it in a high-pressure vessel,” he adds. “The idea would be to send trucks out periodically to haul the gas to the nearest sales line.”
Aldridge says the potential for carbon credits will augment pneumatic lift’s already-strong economics. Noting that the floats in each pump are the only moving parts and that the downhole components are made from stainless steel or high-density polyethylene, he says the system can be extremely durable.
“In Central Texas, we had a chance to put our pumps in wells that required workovers every 10 months on average while they were on rod pump,” Aldridge recounts. “The main causes were pump changes, rod wear and holes in the tubing, as well as corrosion. With our system, there are almost no moving parts and no carbon steel in the well. Today, some of the wells have gone more than five years without requiring any changes.”
For other great articles about exploration, drilling, completions and production, subscribe to The American Oil & Gas Reporter and bookmark www.aogr.com.