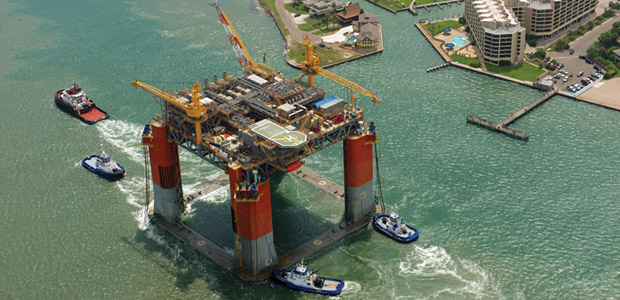
Floating Production Systems
Standardized FPS Design Key To Fast-Track Success At Delta House
By Rick Fowler, Eric Zimmermann, Joe M. Leimkuhler, Craig Mullett, Bruce D. Cooley, Barney P. Paternostro and Jack Boelte
HOUSTON–On April 16, LLOG Exploration Company LLC and its partners commenced production on one of the Gulf of Mexico’s most efficient deepwater developments to date: the Delta House multiple-field project in the Mississippi Canyon Miocene play.
First oil flowed to the new Delta House semisubmersible floating production system moored in 4,500 feet of water only about three years after the first of three anchor fields was discovered, ranking it among the best cycle times for a Gulf FPS-based development. The fast-track schedule included starting the FPS engineering work and the bidding of construction yards prior to even drilling the discovery well: the Son of Bluto 2 in Mississippi Canyon 431. The partners also utilized private equity funding to facilitate the abbreviated timeline for starting construction of the host platform and export lines.
The first phase of operations at Delta House includes the three anchor fields, located between six and 14 miles from the FPS, an Exmar OPTI-11000™ semisubmersible design stationed at Mississippi Canyon 254. The fields produce from Miocene-age reservoirs in a channel levee turbidite depositional environment at subsurface depths of 12,000-18,500 feet. The fields are produced through two in-field flow loops that tie the wet trees and subsea manifolds to steel catenary risers connected to the FPS. A 12-inch oil and a 16-inch gas pipeline export production.
Production is scheduled to ramp up through the end of 2015 as the seven wells already drilled in the area are brought on line. Longer term, at least four more LLOG-operated fields eventually could tie into the host platform.
LLOG is the operator of Delta House, and along with Blackstone Energy Partners (LLOG’s joint venture partner in the Gulf), is the largest working interest owner of the subsea wells. Project co-owners are Red Willow Offshore, Calypso Exploration, Deep Gulf Energy II, Houston Energy, and entities managed by Ridgewood Energy. ArcLight Capital Partners provided construction financing for the $860 million FPS and export pipelines, and is 51 percent majority owner of the host platform.
Borrowing its name from the fictional fraternity in the 1978 movie Animal House, the project symbolizes LLOG’s transition from a Shelf operator focused primarily on mature, shallow-water properties to becoming one of the largest privately owned deepwater exploration companies in the Gulf, and the top privately held liquids producer in the United States.
It is LLOG’s second major FPS-based development to be brought on line in the past four years. The first FPS, using an Exmar-designed OPTI-EX™ hull, was installed at the Who Dat Field in Mississippi Canyon Blocks 503, 504 and 547. As LLOG was about to bring Who Dat on production in the fall of 2011, it recognized that a number of exploration prospects in its deepwater Gulf inventory were “hub class,” meaning that if drilling was successful, field development might include an FPS.
First steel cutting for the Delta House FPS hull occurred in March 2013 at Hyundai Heavy Industries’ yard in South Korea. Dockwise’s Treasure heavy-lift transport vessel delivered the fabricated hull to Kiewit Offshore Services’ yard in Ingleside, Tx., in May 2014 for integration with the deck. LLOG is operator of Delta House. Blackstone Energy Partners is LLOG’s joint venture partner in the Gulf. Delta House co-owners are Red Willow Offshore, Calypso Exploration, Deep Gulf Energy II, Houston Energy, and entities managed by Ridgewood Energy. ArcLight Capital Partners provided financing for the FPS and export pipelines.
Standardized FPS Design
While the industry norm is to custom design each FPS to the needs of a specific discovery, LLOG decided that 15 hub-class prospects in inventory and a consistent exploration success rate of 70 percent warranted a change of philosophy. Consequently, LLOG set out to implement a “design one, build many” FPS project.
To set the stage for efficient fast-track deepwater developments, LLOG’s goal was to develop a standardized FPS design basis that would fit the needs of most of its hub-class exploration prospects. LLOG chose the OPTI design for a number of reasons:
- LLOG prefers a wet tree solution to keep drilling and production operations separate, believing that the benefits of predrilling and completing wells generally outweigh the dry tree advantage of lower intervention costs.
- It had success with the OPTI design at the Who Dat project, and choosing any other design would require additional time to become familiar with the design.
- The design has high flexibility and may be deployed in water depths up to 10,000 feet.
- The design is robust and compliant with the latest windstorm criteria.
- A four-column semisubmersible allows for lower-risk quayside integration compared with other FPS designs that require an offshore lift.
- The single-deck design facilitates construction and allows for late deliveries of equipment without affecting the overall schedule (most deepwater facilities use three decks, and each subsequent deck cannot be floated in place until all the major equipment is in place on the previous deck.
- The hull is designed to use less steel and to be easier to fabricate than other hull designs (in fact, Delta House achieved a ratio of payload to hull steel weight of 1.0).
LLOG elected to design the FPS with a nameplate capacity of 80,000 barrels of oil, 200 million cubic feet of gas, and 40,000 barrels of water a day, with an API oil gravity range of 25-38 degrees and a gas-to-oil ratio range of 750-2,000 cubic feet per barrel. LLOG defines nameplate to exclude standby/redundant equipment. For example, the 80,000 barrels of oil would include three, 40,000 bbl/d pumps so that if one pump was down for maintenance, the facility would still be capable of producing the nameplate capacity.
High run times are expected using the nameplate capacity, and with peaking capacity of 100,000 bbl/d oil and 240 MMcf/d of gas, production beyond the nameplate is achievable. The throughput capacity met the needs of nearly all of LLOG’s hub-class prospects, and is the largest capacity that can be achieved with a single deck lift with existing equipment. LLOG chose to design for ANSI 1,500 exports for both oil and gas, since doing so would be adequate for nearly every pipeline in the Gulf.
Superior Economics
LLOG recognized that the facility would be overdesigned for some of its prospects, but felt the standard design would yield superior economics. A purpose-built design would slow the schedule and sacrifice cost savings, and would not be proportional to capacity. For example, a 20 percent reduction in capacity would reduce construction costs by much less than 20 percent. In addition, LLOG recognized that for an FPS, any excess capacity would be available immediately for third-party processing, which would provide an additional source of revenue.
LLOG also acknowledged the possibility that the standard design might be less than the capacity design compared with a purpose-built facility for some of its prospects. LLOG engineers took comfort in knowing that the proposed standard met the actual peak production for more than 80 percent of historical fields in the deepwater Gulf. In the rare instance when a discovery might produce more than 100,000 bbl/d of oil, LLOG concluded that the schedule advantages relative to a purpose-built facility would lead to superior economics. Also, in that instance, given the original reserve capacity included in the FPS design, the possibility existed to expand the facility to increase capacity.
The deck was mated to the hull in June 2014. The floating of the main deck over the truss and the integrated lift of 9,580 tons were the largest ever performed at Kiewit’s Ingleside yard. LLOG already has begun engineering a second standardized Delta House FPS to be used on a future Gulf discovery.
With this design basis, LLOG believed the standardized FPS would be ideal for most of its hub-class prospects. The one exception would be a discovery with high levels of hydrogen sulfide. LLOG had prospects that anticipated H2S, and understood that the unexpected presence of high levels of H2S in a prospect would require a significant redesign of the FPS’s processing equipment.
Engineering for the Delta House hub-class FPS design began in earnest in October 2011 with more than 100 engineers assigned to the project. At this time, LLOG did not have a single discovery that might need an FPS (the discovery well in what would become the Delta House development area was not drilled for another four months). The hull design was similar to the OPTI-EX design at Who Dat, only larger. The topsides design used a process similar to other LLOG production platforms, but was designed essentially from scratch.
Also in October 2011, LLOG began visiting various fabrication yards to consider a partnership to construct its series of Delta House FPSs. In addition to the customary criteria of yard capabilities, experience, quality and schedule performance, LLOG sought a yard large enough to build multiple units simultaneously, if desired. LLOG planned to build relationships with the yards so that construction engineering would not be required for each FPS, and that lessons learned from constructing one unit could be applied directly to all future units.
As a private company, LLOG is able to sole-source large contracts, if it is advantageous to do so. By December 2011, LLOG had narrowed the number of yards and sent a request for proposal to each finalist to build the Delta House FPS with an option to build a second standardized FPS within a certain period. LLOG requested a firm price for the hull and deck, since the design was known to be similar to the OPTI-EX and the engineering was well understood. Adjustments were allowed if the hull or deck size changed from what was anticipated at the time of the RFP.
Since the engineering had just begun for the topsides and equipment, the RFP requested unit-based pricing on most items (e.g., cost per linear foot of a particular size and grade of pipe) with cost-plus allowed on other items (such as electrical work). After reviewing the proposals, LLOG elected to construct the hull at Hyundai Heavy Industries’ yard in South Korea, and to build the topsides and integration at Kiewit Offshore Services’ yard in Ingleside, Tx.
First Two Discoveries
In February 2012, LLOG and its partners made the first Delta House discovery with the Son of Bluto 2 prospect in Block 431, drilled to a depth of 18,500 feet. The field is a stratigraphic trap on a regional dip, and is in the eastern portion of the Ariel Field depositional system. Son of Bluto 2 was not considered hub-class since its reserves were insufficient to justify constructing a new FPS.
Three months later, LLOG and its partners made the second Delta House discovery with the Marmalard prospect in Mississippi Canyon 300, drilled to 18,100 feet. Marmalard is a turbidite sheet sand draped over a four-way structure with stratigraphic edges. Unlike Son of Bluto 2, Marmalard was indeed a hub-class prospect.
However, with only a single well drilled, the reserve range on this field was quite large. Given the wide range of reserves, most companies operating in the deepwater Gulf would have drilled delineation wells before proceeding with engineering, much less construction.
Construction of the single-deck topsides began in December 2012. The FPS has a daily nameplate capacity of 80,000 barrels of oil, 200 million cubic feet of gas and 40,000 barrels of water, with peaking capacity of 100,000 bbl/d of oil and 240 MMcf/d of gas. The throughput capacity meets the needs of nearly all of LLOG’s hub-class prospects, and is the largest capacity that can be achieved with a single deck lift.
LLOG and its partners considered a number of options to develop the Son of Bluto 2 and Marmalard discoveries, as well as an LLOG prospect at an adjacent lease discovery. The first option was to develop the three anchor fields using existing hosts in the area, which would have required subsea tiebacks of 25-35 miles. While tiebacks of this distance were practical because of the properties of the oil, the additional distance could reduce reserves, depending on reservoir drive mechanisms.
In addition, no single host had enough capacity to handle all three anchor fields, so an existing host option would mean multiple simultaneous projects. The subsea option would work reasonably well at the lower range of the reserve spectrum, but anticipated curtailments at higher reserve scenarios would severely reduce net present value.
A new-build FPS provided superior economics to the host option at the high end of the reserve range, but at the low end, the project did not meet the company’s economic hurdles. Delineation drilling would eventually narrow the reserve range to determine whether adequate reserves were present to proceed with the FPS project, but waiting for the delineation results would erode the project’s NPV.
Private Equity Financing
One of the key elements in Delta House’s success was the decision to use private equity financing to reduce the economic threshold and allow early project sanctioning.
There are several examples in the Gulf where a party other than the owner of the reserves owns the production facility and/or export pipelines, including Devils Tower, Marco Polo, Independence Hub, Tubular Bells, and Thunder Hawk. The main advantage for the producer is that it can use its capital for its core business of exploration and production, rather than paying for infrastructure.
In these transactions, the infrastructure owner provides the upfront capital and then collects monthly fixed fees, along with additional fees based on the amount of production processed through the infrastructure.
LLOG’s understanding was that all these prior transactions involved investment-grade credit of the producer to guarantee a significant portion of the future payments. At Delta House, neither LLOG nor its partners were investment grade. However, LLOG sought an infrastructure transaction with the reserves as the ultimate source of value for the infrastructure owner. LLOG recognized that the infrastructure owner also might perceive value in the potential of hosting yet-undiscovered third-party production, or eventually relocating the FPS.
LLOG began negotiations with ArcLight Capital Partners in May 2012 to ascertain the feasibility of an infrastructure transaction for Delta House. One of the keys to making the transaction successful was a tiered processing fee so that ArcLight could be assured a reasonable return at the low end of the reserve range, and the producers would not have to pay an inordinate amount of processing fees if the high end of the reserve spectrum materialized.
Although the transaction was not yet fully executed, LLOG was confident enough that the deal would be closed that it began purchasing long-lead-time items for the project in July. The ArcLight transaction closed in December 2012, and the remaining construction contracts were executed quickly, allowing FPS construction to begin that same month. Without the ArcLight transaction, the project likely would have been delayed a year to allow further delineation drilling.
Export Lines And Topsides
LLOG reviewed landing point options for both the oil and gas exports for overall flow assurance, capacity assurance, connection cost, counterparty reliability of performance, agreement terms, and overall revenue ($/unit) net back, including transportation and market effects. Most of the options required about 35 miles of new pipe, so connection cost was not necessarily the largest factor.
For oil export, since Delta House oil is sweet, the Shell-operated Odyssey Pipeline system represented the best overall fit. LLOG determined that the optimum oil export system would be a departing oil pipeline rated for a maximum allowable operating pressure (MAOP) of 3,705 psi (ANSI 1,500). An above-water specification break was necessary downstream since the connection to Odyssey had to match its MAOP of 1,440 psi.
The final oil export system had 31 miles of new 12 3⁄4-inch pipe from the Delta House FPS to Enterprise Products Partners’ Viosca Knoll 817 platform in 673 feet of water, and a second five-mile leg of new 12 3⁄4-inch pipe departing from Viosca Knoll 817 and terminating in a hot tap to Odyssey’s line in about 300 feet of water.
For gas export, the BP Pipeline (North America)-operated Destin Pipeline Company’s system was determined the best fit. Gas from Delta House is delivered through 31 miles of new 16-inch line that links the FPS to the 24-inch Destin system.
The Sevan Louisiana is drilling additional Delta House wells this year, with Seadrill’s dual-BOP West Neptune performing the frac pack completions. Both dynamically positioned drill ships are under three-year contracts to LLOG. Production is scheduled to ramp up through the end of 2015 as seven wells already drilled in the area begin producing to the FPS. At least four more LLOG-operated fields eventually could tie into the host platform.
As the laboratory reports became available on fluids from the Delta House wells, it was apparent that one of the fields had unusually high propane and butane. Both are difficult to manage in an offshore environment, since they can cause oil export lines to exceed their Reid vapor pressure or cause slugging in gas export lines. LLOG decided to install a crude stabilization unit to address the problem.
As in most deepwater projects, the topsides weight budget was a challenge already, without the additional burden of a crude stabilization unit. To address the weight issues, LLOG first decided to integrate some equipment that previously had been planned as skid-mounted units built off site. This change increased costs, but saved approximately 500 tons of payload by eliminating the weight of the associated skids. While this helped the weight situation, further changes were necessary.
LLOG decided to relax some aspects of the generic FPS design basis. First, the minimum crude gravity was raised from 25 to 28 degrees, which reduced retention time and vessel size. The crudes from Delta House wells are significantly lighter, so relaxing the specification was not an issue for the fields (if 25-degree gravity oil was delivered to the FPS, the process would still work, but the FPS probably would not achieve its full 80,000 bbl/d capacity, depending on the relative amounts of oil, gas and water).
Second, the gas export specification was relaxed from ANSI 1,500 to ANSI 900, since the gas export destination chosen was ANSI 900. At the Delta House final weigh in, LLOG confirmed it had achieved its goal of 1,000 tons of spare payload.
Construction And Installation
Hull construction went well, with first steel cutting in March 2013 and hull delivery in March 2014. The biggest challenge during hull construction was managing the effects of other projects in the same dry dock, which interfered with the footprint of the Delta House pontoon. The hull was transported from Korea on a heavy-lift transport vessel and arrived in Ingleside in May 2014.
Topsides construction began in December 2012. The deck was integrated onto the hull on June 17, 2014. The biggest challenge with the topsides was the design-while-build process, which was focused on keeping the engineering drawings ahead of construction. Floating the main deck over the truss and the integration lift of 9,580 tons were the largest ever performed at Kiewit’s yard. The fully integrated FPS sailed from Ingleside in September 2014, and all 12 mooring lines were fully installed and appropriately tensioned in October.
Each anchor field is being developed with wet trees flowing to subsea manifolds and then on to the FPS through the two in-field steel catenary riser flow loops. Two of the fields use a single, four-slot manifold with looped six-inch flowlines. Marmalard is being developed with two daisy-chained, four-slot manifolds (allowing for up to eight wells) with looped eight-inch flowlines.
The looped lines allow flexibility to direct a given well to a specific flowline to improve production. The looped lines also facilitate pigging and hydrate removal, if required. Three-phase subsea meters allocate production to individual wells, and electro-hydraulic umbilicals control the wells and convey chemicals to each wellhead.
Delineation And Completion
LLOG drilled an additional well at Marmalard that indicated apparent communication between the discovery well and delineation well over a distance of 3.5 miles. Some new pay zones were found in the delineation well also. As a result of the delineation drilling, Marmalard’s expected reserve range increased significantly.
LLOG also drilled a successful discovery in the third field, and followed that with two delineation wells. With six wells drilled, the low, most likely and high-end reserves for the project more than doubled, compared with distribution at project sanctioning, when only two wells had been drilled.
The first two Delta House wells were drilled by the Noble Amos Runner in 2011-12, the next two were drilled by the Ensco 8502 in 2012-13, and the Ensco 8503 drilled the sixth well in late 2014. The dynamically positioned Sevan Louisiana drilled the seventh well earlier this year, and also is scheduled to drill the eighth and ninth wells in 2015.
The Seadrill West Neptune dynamically positioned drill ship was delivered to Delta House in late 2014, and has performed the majority of the completions. With two blowout preventer stacks onboard, one BOP could be tested and recertified while the other was in use. That saved at least 12 days in completing each well, compared with using a single BOP stack that must be recertified and tested after each use. Both the Sevan Louisiana and the West Neptune are under three-year contracts with LLOG.
Each well was completed with frac packs. Reservoirs with shale breaks between pay zones have multiple frac packs to maximize production and utilize smart-well technology to manage zone changes. LLOG used a single wing to ensure the frac pack would access the formation beyond any near-wellbore damage from the drilling fluids, then opened the reservoir hydraulically and pumped the proppant. Screens keep proppant from entering the wellbore during production. While gravel packs may be adequate, frac packs increase well productivity.
As LLOG learns more about reservoir performance, additional development wells and exploration step-outs are anticipated. The majority of the development work is planned for the dual-BOP West Neptune. Other single-BOP rigs are planned for the riserless portion of these wells, enabling the West Neptune to drill the deeper portions of the wells to total depth, and then to complete with no added downtime for BOP recertification.
Future Plans
A total of seven Delta House wells are being brought on production to the FPS now, with the two additional wells drilling later this year planned in the near term. Since the original execution of the ArcLight transaction, a third-party field (not LLOG-operated) has contracted for processing at the Delta House FPS. LLOG anticipates continued exploration in the area, ultimately resulting in additional LLOG-operated fields tied to the FPS for processing. Ultimately, we expect 15 wells to be produced to the FPS.
LLOG is planning to begin engineering for the second standardized Delta House FPS, which will be used on a future discovery. That engineering effort will include removing the crude stabilization unit, restoring the other design basis parameters to their original values (including oil as low as 25 degrees API gravity and ANSI 1,500 gas export with associated booster compression), and making a variety of other improvements designed primarily to save weight. LLOG also will consider pre-engineering a water injection unit that can be installed on the FPS, once the production performance is understood.
Delta House is truly a “fast-track” project. Key contributors to the accelerated project schedule were concept selection, early start of engineering, yard bidding prior to first discovery, and purchasing long-lead-time items before project sanctioning. Project sanctioning was accelerated by private equity financing of the infrastructure and lowering the producers’ economic threshold so the project could move forward with only two LLOG wells drilled. Implementation of the project went well.
Delta House was designed to be the first of many in a series of similar FPS facilities. The OPTI-11000 hull design and LLOG’s standard topsides design are highly flexible and should be suitable for many deepwater projects. LLOG expects to use the lessons learned from executing each project to make minor adjustments to improve subsequent projects.
Rick Fowler has been the vice president of deepwater projects for LLOG Exploration Company since 2007. He has been involved in multiple Gulf developments using both floating production systems and subsea tiebacks. Prior to joining LLOG, Fowler was employed by Dominion Exploration & Production and Exxon in various operational and supervisory assignments. He holds a B.S. in mechanical engineering from Tulane University.
Eric Zimmerman is vice president of geology at LLOG Exploration. He joined the company in 2007 as a deepwater geologist. Zimmerman has focused his career on exploration and development projects in the deepwater Gulf of Mexico, with previous experience at BP and Dominion. He holds a B.S. and an M.S. in geology from Louisiana State University.
Joe M. Leimkuhler is vice president, drilling, at LLOG. He joined the company in 2012 and has 31 years of experience in onshore and offshore drilling. He began his career working the Wyoming Overthrust Belt as a mud engineer before joining Shell, where he held a variety of roles, mainly in the deepwater Gulf. Leimkuhler holds a B.S. from the University of Montana and an M.S. in petroleum engineering from the University of Wyoming.
Craig Mullett is offshore construction manager at LLOG Exploration. He has served at the company for 16 years, joining LLOG in 1999 after an 18-year career as a facilities engineer at Shell. Mullett holds a B.S. in mechanical engineering from the University of New Orleans.
Bruce D. Cooley is vice president, facilities, at LLOG. He has 24 years of industry experience, including extensive experience in subsea and deepwater development projects. Before joining LLOG in 2001, Cooley worked for Texaco USA and Texaco North Sea UK for 12 years, and was involved in Texaco’s first deepwater development in the Gulf of Mexico. He holds a B.S. in mechanical engineering from the University of Louisiana-Lafayette.
Barney P. Paternostro is a completions/production engineer at LLOG Exploration. With 26 years of experience with major and independent oil companies, he joined LLOG in 2007. During his tenure at the company, he has implemented 16 deepwater subsea completions, 10 of which were intelligent wells with two to three stacked frac packs. Paternostro holds a B.S. in petroleum engineering from Louisiana State University.
Jack Boelte is director of marketing and midstream at LLOG. He joined the company in 1992 and has 20 years of industry experience in marketing. He has served as director of marketing and midstream for the past 10 years. Boelte received a B.S. in accounting from Louisiana State University.
For other great articles about exploration, drilling, completions and production, subscribe to The American Oil & Gas Reporter and bookmark www.aogr.com.