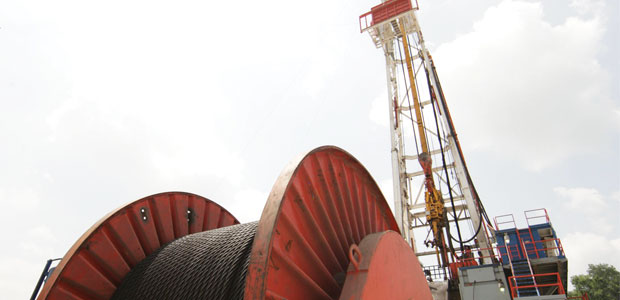
Horizontal & Innovative Drilling
Technologies Enable Ultralong Laterals
By Jeff Boggs, John Pauley, Ahmed Al-Essa and Jorge Guzman
MORGANTOWN, W.V.–In mid-2013, CONSOL Energy Inc. completed drilling operations on the longest lateral drilled to date in the Marcellus Shale. The lateral section of the Kuhns No. 3B horizontal well in Westmoreland County, Pa., drilled 10,684 feet through the Marcellus (19,000 feet total measured depth) in a single run in only 14 days. Earlier this year, the operator broke its own lateral length record in the Marcellus on the NV34G well in Washington County, which drilled a 10,970-foot lateral section to 18,770 feet MD.
CONSOL also has drilled record-setting lateral lengths in the Utica Shale play in Ohio. The reason for extending the lateral length of horizontal Marcellus and Utica wells is simple: The longer the lateral, the more pay zone exposed for completion, and the more pay zone exposed, the more fractures can be initiated in the rock matrix to maximize well productivity. Each of CONSOL’s horizontal Marcellus and Utica wells is hydraulically fractured with 25 to 35 stages to allow completion fluids and proppant to contact as much rock as possible.
But success in shale plays is largely a function of operational efficiency. Accordingly, a key part of the company’s strategy is reducing cycle times from spudding a well to turning it on line to minimize cost while growing production. The objective is to safely drill a high-quality well bore to target depth and complete the lateral section with multistage frac treatments in as little time as possible.
Accordingly, drilling and completion efficiencies are evident throughout the company’s Marcellus and Utica operations. For example, a Patterson-UTI rig under contract to CONSOL drilled four laterals on the NV58 pad between May 1 and May 31. In the second quarter, the company averaged drilling 1,000 feet of lateral every 1.4 days in its Southwest Pennsylvania horizontal program. In regard to completion efficiency, CONSOL completed six frac stages a day in the second quarter on the Gaut pad in Westmoreland County, which compared with an average of 3.5 stages per day in 2013.
For any oil and gas producer, the bottom-line results of any business strategy are measured by one key metric: production growth. In that respect, CONSOL produced 51.9 billion cubic feet equivalent in the second quarter of this year, representing a 34 percent increase over the second quarter of 2013. Net daily production averaged 542 million cubic feet of natural gas, 1,209 barrels of oil/condensates, and 3,514 barrels of natural gas liquids, and the company is on track to reach 60 Bcfe in production in the third quarter.
Enabling Technology
Rotary steerable systems (RSS) is one of the key technologies enabling CONSOL to precisely steer ultralong laterals through shale formations while simultaneously improving drilling efficiencies. In fact, CONSOL was among the first operators to routinely use RSS in the Marcellus play to optimize performance by maximizing the wellbore’s contact with the reservoir and shorten the rig time to reach total depth.
CONSOL Energy Inc. has drilled record-setting lateral lengths in both the Marcellus and Utica shale plays. Last year, the company drilled a 10,684-foot lateral in the Kuhns No. 3B horizontal well in Westmoreland County, Pa., in a single run in only 14 days. Earlier this year, the company again set a Marcellus lateral length record on the NV34G well in Washington County, Pa., drilling a 10,970-foot lateral section (18,770 feet MD).
Combined with high-efficiency PDC bits, state-of-the-art high-build-rate RSS technology provides an effective solution to drill the tangent, curve and lateral sections in a single run with high build rates, superior directional control, longer tool run life, improved penetration rates, and enhanced durability and drilling efficiency.
Historically, drilling wells in unconventional plays often has meant operators had to choose between drilling a well quickly or drilling it accurately. For shale wells, building the curve from the vertical to the horizontal takes time and space, both of which impact the return on investment. Not only must operators drill tighter and smoother curves to ensure that the entire well stays within their lease lines, but they must be able to drill out the lateral section to target depth as quickly and efficiently as possible.
Meeting these dual requirements was the primary goal in developing high-build-rate RSS technology specially designed for land wells that require higher buildup rates and smooth wellbores. The latest generation of closed-loop RSS tools incorporates several proven design features that deliver tighter curves, less tortuous well paths, and maximum contact with the pay zone.
Rotary steerables were deployed initially in offshore applications, given the sizeable value they can deliver at higher spread-cost environments. As the technology matured, its value became apparent in maximizing value and cost savings in onshore wells, especially those in horizontal unconventional plays. The ultimate goal is to combine the vertical, curve and horizontal sections in a single fast run.
The RSS system used to drill the record lateral lengths in CONSOL’s wells features a unique steering design that provides precise control and enhanced performance in a range of formations and environments. Three expandable, external pads are mounted on a short, slow-rotating sleeve close to the drill bit. The pads apply a continuously adjustable deflection of the drill string while it continues to rotate.
The pads are controlled with information provided by a near-bit inclination sensor, an internal closed-loop control system, and a measurement-while-drilling module, which relays data to the surface. The closed-loop system automatically reviews and adjusts steering forces every second, according to the tool position, to ensure superior hole quality with minimal tortuosity compared with “overshoot-and-correct” or “randomize” methods. This ultimately allows for smoother drilling and an easier completion operation.
Changes to the well path can be downlinked to the system, and confirmed and saved by the downhole components. Because the sleeve is decoupled from the downhole dynamics of the bottom-hole assembly, the steering unit remains stable to ensure precise steering even if the BHA encounters a stick-slip condition. Moreover, the RSS optimizes hydraulics and hole cleaning, with the steering mechanism operating independent of bit hydraulics and pressure drop.
Greater Reliability
Thanks to advances in PDC drill bit hydraulic and mechanical design, and premium cutter technology, RSS also gives the driller greater reliability with improved rates of penetration. Combining a more efficient bit design and polished cutters with RSS technology gives operators with a huge drilling performance improvement. Premium diamond cutters decrease friction on the cutter face for increased durability, wear resistance and run life.
Enhanced durability is particularly important when building long tangent sections leading to the curve. Some formations in the tangent section of Marcellus and Utica wells are particularly challenging, but the polished cutters and the hydraulic and mechanical efficiencies designed into advanced PDC bits allow them to withstand the wear for longer run life. Plus, the cuttings size is smaller for easier transport to surface in ultralong laterals, and the tendency for cutter balling on the bit is reduced, which improves cutting evacuation and penetration rates.
The ability to more efficiently move cuttings out of the hole, coupled with the continuous rotation of the drill string, helps minimize torque and drag, allowing longer lateral step-outs to be built. Apart from drilling an extended-reach lateral in less time and in fewer trips, advanced RSS technology benefits subsequent completion activities and overall field economics through improved well bore cleaning–allowing casing to be run in the hole faster and improving wellbore integrity–and continuous drill string rotation, which eliminates frequent transitions from sliding to rotating.
Continuous rotation prevents micro-ledges from forming in the wellbore for smooth casing running and results in a more consistently sized borehole, saving on the volume of cement and time required to complete a cement job. Other completion activities, such as running plugs and perforating, also benefit from a smooth wellbore.
The precise, continuously adjustable steering mechanism helps the driller stay in the desired target zone and avoid the “porpoising effect,” in which the wellbore contains many tortuous, up-and-down directional changes. A less tortuous well path may improve production by minimizing valleys in the wellbore, where produced water can collect and trap gas production from efficiently moving through.
Planning For Success
Before adopting high-build-rate RSS and PDC bit technology, the typical scenario for CONSOL called for drilling the vertical and curve sections with a motor and then tripping out, replacing the motor with a rotary steerable assembly and tripping back in to drill the lateral. Not only did this require at least two bits to drill the tangent and another for the curve and lateral, but it also added significant tripping time, cost and risk associated with stuck tools.
Reducing cycle times from spudding a horizontal well to turning it on line for production is integral to CONSOL’s Marcellus and Utica strategy. In the second quarter, the company averaged drilling 1,000 feet of lateral every 1.4 days in its Southwest Pennsylvania Marcellus program. Combined with high-efficiency PDC bits, high-build-rate rotary steerable technology enables CONSOL to drill the tangent, curve and lateral sections in a single run for maximum drilling efficiency with superior directional control and improved rates of penetration.
Some of the company’s early wells experienced slow penetration rates, a lot of sliding while trying to kick off into the curve section, and lower-than-desired build rates. It sometimes took 800 to 1,000 feet of wasted space just to build the curve to the lateral.
The objective of developing a more efficient drilling program capable of drilling a well in a single run began with intensive preplanning and modeling. Once it was established that an advanced high-build-rate RSS could drill a well in one run, in-depth reviews of the drilling plan were conducted and the wellbore was modeled with the initial design parameters.
The preplanning stage also included running a series of drilling scenarios in the model, including potential complications caused by excessive torque or geological and geomechanical changes with depth. If the model flagged a particular scenario as high risk, alternative drilling parameters or wellbore design was developed to minimize the risk.
Changes to the basic 8¾-inch PDC drill bit design enabled it to drill through the planned 4,000 feet of vertical section and then continue drilling the curve and lateral in a single run. By understanding the geology of the different sections and the desired build rate, modifications were made to the six-bladed bit with ¾-inch cutters and backup cutters that represented the latest generational advancements used successfully on other Marcellus wells.
Preplanning meetings uncovered the need to run the RSS with a motor assist, which alleviated the high torque expected when drilling out a long lateral section. This helped extend the operating life of the pipe and the rig’s top drive. The plan also included any changes required in the drilling fluid system, such as the need for additives to reduce torque. As it turned out, those changes were not needed, but they were ready as a contingency.
The motor-assisted high-build-rate RSS system fitted with a PDC bit with premium cutters immediately proved its potential, once deployed on the well site. The near-bit gamma ray measurements helped predict formation conditions just ahead of the bit. Those measurements were coupled with near-bit inclination measurements and results from the 3-D model to better predict where the next 30 to 50 feet of borehole should be drilled. It also helped the BHA stay in the sweet spot and avoid going out of zone, which, obviously, would hinder forward drilling progress.
Drilling A Record Lateral
The first well drilled was the record-setting Kuhns 3B. By eliminating two bits and two extra trips in and out of the hole, the RSS system saved several days of rig time. It also achieved a build rate in the curve of 15 degrees per 100 feet, a significant improvement over the 5-6 degrees/100 feet build rates for conventional rotary steerable systems.
Not only is the technology allowing CONSOL to achieve the desired build rates in the curve section, but it also is helping the company make faster directional changes in the lateral sections. Some laterals run through complex geologies with faults and dips, and the ability to make 8 degrees/100 feet turns in the lateral is a major advantage.
CONSOL has added the high build-rate RSS on two other rigs in the Marcellus and one in the Utica, and is continuing to experience predictable high performance while drilling new wells. The technology has changed the company’s business model with regard to its expectations of how fast a well can be drilled. Greater predictability in how long it will take to drill the curve and lateral in a new well allows the operator to better estimate costs, and ultimately, deliver more wells in a shorter period.
CONSOL has progressed from drilling a Marcellus well in 21 days on average to eight to 10 days, while the average lateral length has increased by 60 percent. During the second quarter of 2014, average lateral lengths varied from 6,600 to more than 9,250 feet in its Marcellus operations in Pennsylvania and West Virginia, while laterals averaged 9,510 feet in its Utica wells in Ohio.
The Kuhns 3B and NV34G horizontal Marcellus wells demonstrate both the productivity and efficiency gains operators can achieve by leveraging innovative drilling and completion technologies. However, it should be noted that this kind of success story would not be possible without collaboration between the operating company and service company. Success in developing unconventional resource plays in the most efficient and cost-effective manner possible depends on teamwork as much as technology.
JEFF BOGGS is vice president of drilling at CONSOL Energy Inc., where he manages the company’s horizontal Marcellus and Utica drilling programs. Before joining CONSOL in 2007, he served for 15 years as drilling manager at BNG Producing and Drilling. Boggs holds B.S. in petroleum engineering from West Virginia University and a master’s in environmental/environmental health engineering from Marshall University.
JOHN PAULEY is account manager for drill bits in the Northeast U.S. land market for Baker Hughes. Before assuming his current position in 2010, Pauley was a technical field representative for Baker Hughes, specializing in drill bit sales and service in the Appalachian region. He holds an associate’s of science in civil drafting and civil engineering CAD/CADD from West Virginia State College.
AHMED AL-ESSA is global marketing manager for directional drilling at Baker Hughes in Houston. He has been with Baker Hughes since 2006, and previously served as product manager for advanced drilling systems, operations support manager for drilling systems in the Middle East region, Middle East university recruitment team lead, field service manager, and MWD/LWD field engineer. Al-Essa holds a B.S. in mechanical engineering from King Fahd University of Petroleum & Minerals.
JORGE GUZMAN is engineering manager at Baker Hughes, where he supervises the technical team in the Central East area. He previously served at Baker Hughes as a drilling applications engineer in the Northeast U.S. region, an in-house drilling applications engineer and liaison to Gastar Exploration, and an in-house well planner for both the U.S. and Mexican markets. Guzman holds a bachelor’s in mechanical engineering from the Instituto Tecnológico y de Estudios Superiores de Monterrey.
For other great articles about exploration, drilling, completions and production, subscribe to The American Oil & Gas Reporter and bookmark www.aogr.com.