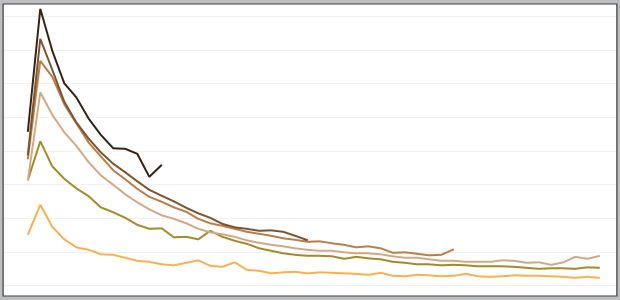
Refrac Facts
Technology Key To Enabling Refracs
By Jamie Phillips
HOUSTON–Unconventional oil and gas wells typically exhibit steep decline curves, and the only way operators have been able to maintain or grow reserves has been to drill and hydraulically fracture large numbers of new wells, leading to substantial growth in U.S. tight oil production. Of course, that growth has been based almost entirely on horizontal wells completed with multistage frac techniques that produce at high initial rates but decline rapidly.
Consider, for example, the Eagle Ford Shale, which the U.S. Energy Information Administration reports has the highest average per-well productivity of any U.S. tight oil play. While the average initial production rate more than tripled between 2010 and 2013, the first-year decline averaged 69 percent in 2013, according to data from Drillinginfo (Figure 1). Moreover, second-year declines have increased significantly in the Eagle Ford, averaging nearly 50 percent for wells drilled in 2013.
At those rates, a well that came on line in April 2013 with an IP of 350 barrels a day was yielding about 110 bbl/d by April 2014, and would now be making on the order of 55 bbl/d, representing an 84 percent loss of productivity within 24 months of starting production.
With historically high oil prices and plentiful prospects making aggressive drilling programs feasible over the past several years, the strong IPs of new wells more than offset the characteristic steep decline curve of existing wells.
FIGURE 1
Eagle Ford Horizontal Well Decline Curves in
First 48 Months of Production (Including All Subplays,
and Oil, Wet Gas and Dry Gas)
The furious pace of unconventional development has slowed with falling oil prices. Operators are finding the time to think about ways to improve and extend production from wells in which they already have invested millions of dollars apiece to drill and complete.
With hopes of adding low-cost production and reserves, while boosting estimated ultimate recovery, there is a lot of talk about refracturing wells in unconventional plays. However, the reality is that refracturing is still in its infancy, and the industry has much to learn about refrac engineering best practices and technology solutions before refrac campaigns can be expected to add significant reserves. The situation is not unlike the ongoing learning curve associated with optimizing the multistage frac techniques developed over the past decade for horizontal shale plays.
Unfortunately, however, some of the completion techniques that made shale development possible also make economic refracs difficult to achieve in these plays. But the future will be different as new-generation tools are employed and operators engineer initial frac treatments with the understanding that productive wellbore intervals may need to be accessed at some point to pump a refrac.
Biggest Obstacle
To date, a few operators have attempted refracturing on a limited scale and with mixed results, and numerous papers and articles have been written about various aspects of restimulation: candidate selection, optimum time to refrac, reservoir pressures, refrac design, in situ stress reorientation, etc. However, the biggest obstacles to successful restimulation are finding a way to isolate sections of the wellbore to be treated and delivering the stimulation treatment with high enough rates and pressures to be effective.
Whereas conventional wells are completed to accommodate future remediation, this has not been true for unconventional wells. To speed production and maximize economics, operators relied on methods that accessed the formation as efficiently and inexpensively as practical, starting with plug-and-perf techniques, which were later joined by open-hole completions with packers and ball-drop sleeves. Future refracs simply were not part of the completion plan.
To be fair, there have been virtually no restimulation technologies available to be considered. That could be changing, however, as new completion technologies enter the market.
In theory, refracs make a lot of sense. There are hundreds of thousands of existing wellbores in unconventional formations. Some percentage of those wells should be potential refrac candidates, and recompletions should cost less than new drills. It is known that there are a lot of reserves in place–more than 90 percent of the original reservoir content in tight formations–bypassed by the original completions. In fact, a successful refrac can restore production to levels on par with the IP rate. Finally, restimulation is a proven technology that works well in conventional vertical wells.
Properly executed, when refracturing in unconventional wells:
- New fractures along the lateral should contact virgin reservoir rock. Many wells completed in the early days of the shale boom suffered from poorly designed or incorrectly placed fracs. As a result, pay zones were missed or not stimulated to their full potential.
- Existing fractures should extend to contact untapped formation. It is believed that stress reversal effects can reorient the fracture extensions to propagate perpendicular to the original fractures, adding significant reservoir contact.
- It should restore the conductivity of the original fractures and clean up near-wellbore damage, which can improve well performance dramatically. Studies have shown that, over time, proppants break down under formation stresses, and asphaltenes and fines settle into critical conductivity pathways, resulting in premature production declines.
Unfortunately, all these require effective zonal isolation and a lot of hydraulic energy, and wellbore issues from the original completion make those very difficult to achieve in practice.
Refrac Wellbore Issues
The original stimulations could be accomplished with sheer brute force because there were few, if any, wellbore issues. With new pipe and no restrictions or leaks, rates and pressures could always be matched to the job, and stages were easily isolated for stimulation. That is not the case with refracs. Existing wellbores are full of perforations, and in the case of open-hole completions, often are full of ball-seat/sleeve restrictions. Each of these completion methods presents its own obstacles that must be overcome for a refrac to be successful.
By nature, wells completed with plug-and-perf methods present significant wellbore-integrity challenges. The casing or liner is riddled with holes, making pressure control, zone isolation, and fluid circulation economically impractical, if not impossible.
Open-hole completions with ball-drop frac sleeves have no cement or other barrier behind the casing string; the original stimulation was allowed to flow behind a long section of casing and enter the reservoir through the path(s) of least resistance.
This type of completion presents three problems for restimulation. First, because there is so much open formation outside the frac sleeve, the secondary treatment will not be effective at the lower rates that can be pumped through a straddle system; the available force cannot be focused. Second, interzone communication past isolation packers is not uncommon, and there is a high chance of full communication to the zone above the refrac straddle assembly. This could introduce enough debris on top of a refrac bottom-hole assembly to lead to extensive fishing operations. Finally, with open communication behind casing, there is a heightened well control risk with a straddle assembly in the well.
Although most ball seats can be milled out, any remaining restriction or milling damage can prove problematic for refrac straddle tools. Seals on straddle systems are prone to getting stuck in restrictions, and the jagged and unpolished inside diameter of a milled sleeve can ruin the seals.
The completion method most conducive for refracs appears to be a relatively new technology that represents only a tiny fraction of unconventional completions to date: single-point, cemented completions. This method combines cemented casing and frac sleeves with a coiled tubing-deployed completion tool that isolates each stage for single-point stimulation. The advantages for refrac are the full-drift wellbore, easily located and isolated stages, and a cemented annulus that prevents communication between stages.
For existing wells, refracs must be performed using a straddle assembly, but the frac rates typically are sufficient, thanks to the single-point injection. Also, new stages can be added using sand-jet perforating. However, it is still important to secure the wellbore above the target zone in case the refrac treatment manages to communicate through the formation to the stage above.
Limited Options
Unfortunately, even for promising candidate wells, currently available refrac options have some challenging limitations. Complications can quickly lead to cost overruns, project abandonment because of mechanical problems, and even loss of a well. However, as refrac demand grows, the industry surely will respond with new technology and techniques, just as it did at the outset of the shale revolution.
But for now, there are only a handful of ways to address the wellbore problems: squeezing off all perforations with cement, installing expandable steel liners, pumping permeability modifiers and temporary blocking agents, and using a coiled tubing straddle assembly. The method used depends on the nature of the formation and the condition of a particular well.
To restore pressure integrity, perforations could be sealed off with cement squeezes. The cost can be prohibitive except, perhaps, for older completions with short laterals and few stages. It is also unlikely that the squeeze would withstand a high-pressure, high-rate frac.
Expandable steel liners have been installed to create a fresh wellbore through the lateral section. The drawbacks are high cost, reduced collapse rate and the reduced inside diameter of the liner, which limits recompletion options. However, expandable scab liners can accommodate higher pumping rates for a plug-and-perf recompletion.
Biodegradable balls, gels and particulates have been used with some success to seal all but the target zone, allowing a treatment to be pumped. This method assumes that the bridging material will follow the path of least resistance, which would be perforations that received the initial frac. With that path temporarily sealed by a blocking agent, the subsequent refrac would be diverted to perforations that did not take fluid during the original completion. Demonstrated limitations are the requirement for fluid circulation and positive wellbore pressure, uncontrolled placement, highly variable and unpredictable performance, short effective life, high cost, high risk and low success rates.
Straddle packers on coiled tubing can be used to isolate target intervals, with the stimulation pumped through the CT string. A key drawback of straddle assemblies is that treatment rates are limited to about 18 barrels a minute or less for the largest (2⅞-inch) coiled tubing, and there is still a need to seal the wellbore above the target zone to prevent communication through the formation, resulting in inflow on top of the straddle assembly. This method, however, does overcome many of the wellbore issues, and the low pumping rate is somewhat offset by the single-point stimulation.
Reclosable Sleeve Technology
For restimulation to become a practical life-cycle consideration for unconventional wells, new completion technology is needed that maintains wellbore integrity and enables stage-by-stage access and pressure management over the full life of the well. One such solution, now poised to enter the market, incorporates full-drift, cemented casing sleeves that can be cycled open and closed as needed during refrac operations, and also during the original completion and the production phase of the well.
For refracs, the sleeves can be closed using a CT-deployed work string, allowing the wellbore to be filled with fluid for circulation and pressure control. The refrac operation can be performed the same way as the original completion, using similar rates and pressures to deliver enough energy to reopen and extend existing fractures. The secure wellbore also allows new fracture stages to be added using sand-jet perforating.
In addition to facilitating refracs, reclosable sleeves offer important benefits during the initial completion. They can be closed immediately after each frac to allow fracture “healing” and to enable alternate-stage fracturing (the “Texas two-step”) to offset the effects of stress shadowing. Moreover, during production, the sleeves can be closed to shut off thief zones or unwanted water or gas production, or to balance production along the lateral.
Reclosable sleeves have been run and tested already in many wells and have proven to be effective for shutting off water production. It will not be long before operators learn whether reclosable sleeves are the key to effective, practical and profitable refracs.
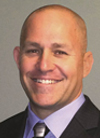
Jamie Phillips is product line manager for refrac systems at NCS Multistage LLC. He has worked in the oil and gas industry for more than 15 years and has experience in manufacturing, engineering, sales, operations and business development. Phillips has knowledge of most of the significant North American oil and gas plays, including the Bakken, Haynesville and Eagle Ford. He holds a B.S. in mechanical engineering from Texas A&M University and an M.B.A. from Texas Christian University.
For other great articles about exploration, drilling, completions and production, subscribe to The American Oil & Gas Reporter and bookmark www.aogr.com.