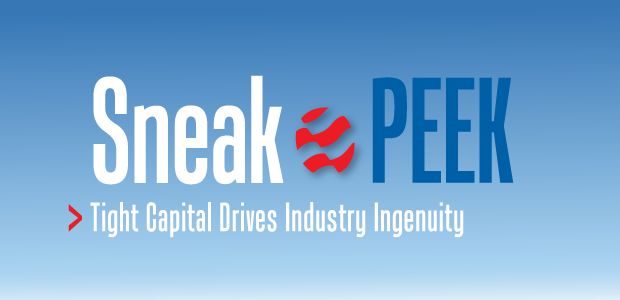
Resource Science
Tight Capital Drives Industry Ingenuity
By Colter Cookson
In response to ongoing investor demands and an uncertain commodity price environment, the industry has shifted from focusing on production growth to emphasizing profitability and delivering returns to investors. With limited capital coming in from external sources over the past year, many producers are relying like never before on producing wells to fund their operational activities.
To reduce those wells’ operating costs and increase their production, producers and service companies are digitizing equipment to collect more data from the field and developing artificial intelligence algorithms that automatically translate that data into meaningful recommendations. Other cloud-based systems are streamlining the tasks associated with requesting, managing and paying for field services.
While some of the industry’s sharpest analysts see higher prices ahead, the innovations applied to tighten belts during this time of austerity may be critical to the industry’s longer-term health and improved profitability, suggests John Gibson, chairman, chief executive officer and president of Flotek Industries.
“Between unconventional oil and gas, the rise of wind, solar and geothermal energy and emerging alternatives such as hydrogen, we live in an age of energy abundance,” he says. “Given the pressure that puts on prices, I doubt we see $100 oil again based on demand alone.”
But with the right technological solutions in hand, $100 oil is not necessary to capture value and drive strong profit margins, Gibson continues. “If producers and services companies work together, the U.S. oil and gas industry can drive costs down and make unconventional reserves profitable at lower price points,” he comments. “We have the drive, ingenuity and technology to provide high-paying jobs that supply essential energy and promote U.S. energy security. In the process, we will not only benefit the United States, but pioneer technologies that can help other countries tap their reserves and improve their quality of life.”
Consolidation will be one component of driving down costs in resource plays, Gibson states. “The mergers between Devon and WPX, Pioneer and Parsley, ConocoPhillips and Concho, and EQT and Chevron Appalachia are creating companies with the economies of scale and compelling assets to get more from their investments. I think the wave of consolidation will continue for a while among both producers and service companies, and it is a healthy and positive step in the quest for greater profitability,” he says.
At the same time, technological advances also will contribute to cost reductions, Gibson predicts, noting that many of them will be fueled by artificial intelligence. “For example, within the next five years, I think we will be able to infer information about downhole drilling dynamics by using cameras to watch how the drill pipe is rotating and slipping at surface,” he offers. “This could reduce the need for expensive sensors.
“While drilling speed and consistency will continue to improve, they already have been optimized to such a degree that the industry will shift its focus from maximizing speed to getting more information during drilling,” Gibson assesses. “There are startups and established companies that already use data from the bit to identify natural fractures and map variations in rock quality so completion engineers can place stages in the best spots and use the right pressures and flow rates for each one.”
Flotek Industries reports it is developing chemistries that can alter pores’ relative permeability to oil, gas and water, enabling producers to target whichever hydrocarbon will be most valuable while reducing their water cut.
Right Chemistries
Gibson adds that gathering more robust data during drilling can help engineers identify the best chemistry for each specific downhole environment. And the right chemistries can change pores’ relative permeability to oil, gas and water so that producers get more of the product they want most, he mentions. “For example, a producer may try to encourage oil rather than water to flow through the pore space by altering surface tension and wettability. The operators that do this well are seeing significant uplifts in oil production.”
Similar techniques can help water from injection wells move through pore spaces and sweep the reservoir more effectively, Gibson reports.
“In 10 years, chemistry combined with advanced data analytics may even enable producers to target individual facies for the fractions of an oil barrel that are most valuable, meaning they could get more of the diesel component or the gasoline piece based on prices,” he remarks.
To reduce downtime on producing wells, Gibson predicts the industry will deploy automated chemical injection as a form of preventative maintenance. “The goal is to move from allowing scale and paraffin to build up so much that the well needs to be shut in and hot oiled or worked over, to continuously monitoring and selectively injecting chemistry to keep scale and paraffin from forming,” he outlines. “As long as the chemistry is effective enough to work quickly in small doses, this should be much more affordable, and it will lower safety and environmental risk.”
Another area of focus for Flotek is developing and refining green chemistries. “Given investors’ interest in ESG and the change in the presidential administration, we think more producers are going to look for safer alternatives to traditional chemistries,” Gibson says. “In many cases, these substitutes work as well or better than their predecessors and are available at a comparable cost.”
As an example, Gibson says solvents based on orange peels can replace xylene, which can burn skin and irritate respiratory systems under prolonged exposures. These organic solvents are more effective than xylene, and once liability is factored in, they cost less, he claims.
“When we talk with executives about replacing xylene, we often see quick action,” Gibson says. “These executives want to protect their employees and minimize their long-term liability, and they understand that safer chemistry will help them meet institutional investors’ ESG criteria and position their company to be acquired by majors.”
Streamlining Completions
Much of the cost to complete a well comes from the time water haulers spend unloading or waiting for a chance to unload, says Dean Grose, CEO of Comtech Industries. “With 300-500 trucks coming to the pad each day during completions, it’s common for trucks to get backed up and to spend three-five hours waiting for their turn to unload,” he details. “The standby charges associated with that add up.”
Comtech Industries’ water unloading system shortens trucks’ unload times from 20-25 minutes to six-seven, the company reports, noting this cuts costs associated with keeping trucks on standby as they wait for their turn to unload. On pads with sufficient space, the trucks connect to the system by driving through open stalls rather than backing up, a change that improves safety and efficiency.
To minimize standby time, Grose reports Comtech has developed two systems. The first shortens the average time to unload each truck from 20-25 minutes to six-seven, while the second minimizes the number of trucks required by helping drivers fill their tanks to capacity. Both systems work together, and they can be equipped with a probe that measures condensate concentrations in real time to keep water with unsafe concentrations away from employees and equipment, Grose adds.
“The key to our unloading system’s speed is that we figured out how to hook the trucks to a common manifold,” he relates. “When that has been tried before, unload times would lengthen to as much as two hours because the water from the trucks with the highest pressure would equalize by moving to ones with lower pressure.”
The pump would also need to be replaced frequently because the air the trucks pushed into the lines as they emptied would hit the pump and cause cavitation.
Comtech’s system addresses both issues while unloading trucks in six-seven minutes and capturing the data the operator wishes to track automatically so employees can spend time on other tasks, Grose says.
On pads with enough space, trucks connect to the system by driving into stalls that have the manifold buried beneath them. Inside the stall, they connect to the system, push a button or use embedded load information capturing technology to start unloading, wait until the system says they are empty, and then disconnect and leave by driving forward, Grose describes. He points out that this approach eliminates the safety risks and time associated with backing trucks up.
When using the embedded information technology to start the unloading process, the system can automatically capture the driver’s name, where the water came from, and how much was unloaded, then transmit that data to the cloud to help the operator and service company monitor key performance indicators.
Accurate Volume Measurements
Comtech’s radar-based system for determining how much water is in trucks’ tanks is extremely accurate, Grose reports. “This is a tremendous benefit because it allows trucks to carry more water in each load,” he says. “We have run trials with 15 trucking companies, and all of them hauled seven to 10 barrels light.”
In the first trial, the trucks averaged 6.89 barrels less than their true capacity. With more accurate water level monitoring, they went from needing 721 loads to 682 and saved the operator $9.34 million a year, Grose relates.
“This underloading was a result of technical limitations, not negligence,” he stresses. “In the past, truck drivers would have to use indirect measurements, such as counting five seconds past the top sight glass or watching the amount of pressure on their axles, to guess when their truck was near capacity. They had to be cautious, because if they put too much water into the tank, the excess would get into the blower and they’d be looking at a $6,000 repair bill.”
Grose says truckers’ indirect measurements perform poorly in part because previously unknown variations in the tank manufacturing process mean that tanks with a nameplate capacity of 110 barrels hold somewhere between 106 and 116 barrels.
By measuring trucks’ true capacity and using a proprietary and patented method that takes it into account, Comtech’s water gauge achieves previously unseen resolution and a guaranteed accuracy of 99.9998%, Grose says. “This lets the operator know exactly how much liquid is on each truck,” he remarks.
That precision has allowed Comtech to develop a system that prompts the driver at certain points during the filling process to ensure the truck always is within 0.2 barrels of the scrub point without going over. This approach allows a full truck without spilling liquid or damaging the pump, Grose says. Alternately, the system can short fill a truck accurately to meet load limits. For example, a truck that is picking up water in Pennsylvania but delivering it to Ohio can be short filled to Ohio’s lower legal amount.
In addition to preventing underloading, Grose says understanding a truck’s true load capacity can help operators track where water moves more precisely. “In the past, everyone had to assume a 110-barrel truck moved 110 barrels of water. Since that does not actually happen, regulators would see discrepancies between reported water volumes at various points and occasionally fine operators for losing water they never had,” he points out.
According to Grose, most water tanks contain some condensate. If condensate levels get too high, static electricity can ignite the water and hurt employees or damage equipment. Based on laboratory tests that involved trying to ignite water with various concentrations, Grose says the danger point is somewhere between 100 and 200 parts per million, with no risk below 100 ppm.
“The traditional way to detect condensate in the field is a paste that can be put on a stick and dipped into water. If the paste changes color, condensate is present,” Grose explains. “This works, but it takes time and offers no indication of how much condensate is present. To give operators a way to measure condensate levels in real time, we developed a probe the size of a dill pickle that is accurate down to 1.0 ppm.”
These probes can be installed at loading or unloading sites and connected to automation systems to keep water with too much condensate from entering or leaving the truck, Grose says. He notes that some clients are collecting and selling the condensate as well.
Optimizing Producing Wells
As investors and banks have become less willing to provide capital to oil and gas companies, optimizing producing wells to increase their profitability has become more important, emphasizes Darcey O’How, business development and education services manager for artificial lift technologies at ChampionX. “Producers have had to turn producing wells into a cash register that can fund their operations, which means finding ways to boost production, minimize downtime, and cut operating costs,” he says.
Given how rapidly conditions in unconventional wells change and how many wells each production engineer needs to oversee, O’How suggests the best way to monitor and optimize well performance is to automate routine tasks and collect the data needed to deploy AI algorithms.
“We have worked on projects where we have been able to reduce operating costs and/or failure rates by 25% or more with the analog tools available today,” he observes. “With AI, we can scale some of that optimization across entire fields. The optimization algorithms may only increase production from each well 2%-3%, but because they can be applied to hundreds or thousands of wells, that adds up.”
For AI to yield results beyond traditional automation, the algorithms need to be based on high-resolution data that is relevant and trustworthy, offers Peter Maly, a senior technical consultant with ChampionX. He adds that they must consider the characteristics of specific fields, including their production histories, pressures and temperatures.
“Maximizing AI’s potential will require collaborative efforts between service companies and producers,” Maly says. “To build an algorithm that can optimize electrical submersible pump efficiency or chemical treatment programs across a field, we need information such as depths, temperatures, pressures, the types of sands and shale the wells produce, and in situ water characteristics.”
Early models suggest AI will be quite powerful, Maly says. He notes the company has test models in place for large Permian Basin operators that adjust chemical dosage rates based on real-time information and weekly or monthly lab analyses.
Materials Science
Material selection is used to extend artificial lift equipment’s life, O’How notes. “We are looking outside traditional solutions to make materials more resilient to operating conditions,” he remarks, noting that ChampionX has partnered with Modumetal to explore the benefits of applying nanolaminate coatings.
ChampionX is writing machine learning algorithms that can optimize artificial lift equipment operation and production chemical dosages. By looking at hundreds or thousands of wells across a field, the company predicts these algorithms will increase production significantly.
Maly adds that ChampionX’s artificial lift engineers and chemists work closely together to ensure they are applying the right metallurgy for specific applications. “When our customers are entering new fields or expanding existing fields, we do detailed analysis on the chemistry to see what problems the equipment is likely to encounter down hole–such as corrosion from carbon dioxide or embrittlement from hydrogen sulfide–so the artificial lift engineers can make informed decisions,” he relates.
When equipment fails, the teams collaborate to determine the root cause and recommend changes to the equipment, the chemical program or the operating parameters that will extend future systems’ run time. “We are building tools, processes and infrastructure that will help us evaluate failures and identify the best corrections more quickly,” Maly reports. “For example, we have a team that is trying to get the time for Permian Basin ESP failure analysis from one or two months to one or two days. This will involve sending artificial lift technicians and chemists to the site to gather samples, mailing them to a laboratory, performing the analysis overnight, and sharing the results digitally so they can be interpreted and applied.”
Maly says this work is a response to customer requests for faster turnarounds.
Digitizing Compression
To improve the uptime and efficiency of its compression fleet, CSI Compressco is deploying a proprietary suite of technologies to enable higher fidelity data transmission from its fleet of compressors, according to Roy McNiven, the company’s senior vice president of operations and manufacturing.
CSI Compressco is deploying technologies and equipment to get higher-fidelity data from its compression fleet. According to the company, this data is enabling machine learning algorithms and trend analysis that are helping it provide greater reliability and better service to customers.
“We are rolling out a telemetry system that sends information every minute, a vast improvement from the legacy system’s transmission rate,” he details. “This will provide us the large quantities of high-fidelity data needed to power machine learning algorithms to enhance predictive maintenance and help us provide better service to customers.”
According to McNiven, these algorithms often enable the company’s reliability center to identify potential problems with compressors several days before they cause downtime or other issues. He points out that the algorithms can identify subtle warning signs that would be hard for an engineer to notice.
“This will provide immeasurable value to customers,” McNiven relates. “If we know a component has a high chance of failing four days from now, we can call the customer and ask when it would be best for us to repair it. Instead of dealing with a sudden failure, the customer can have us come out during other routine or planned maintenance to maximize the site’s uptime.”
McNiven adds that the machine learning algorithms and high-fidelity data help its reliability center diagnose issues accurately enough to dispatch technicians with the necessary parts and tools to avoid multiple trips and resume operations faster. The algorithms also codify knowledge that might otherwise be lost as experienced hands retire.
McNiven points out that CSI Compressco is working with Houston’s Rice University D2K (Data to Knowledge) Lab to develop and refine its machine learning algorithms. “I have enjoyed working with D2K’s team of young engineers and data scientists. They have done a fantastic job of supporting us,” he praises.
To get data from the field to the cloud, CSI Compressco uses a trimode gateway that automatically switches between two cellular networks and satellite communication to maximize uptime and reliability, McNiven notes.
“Rather than reinventing a customer dashboard, we partnered with Caterpillar to display our data in Cat® Remote Fleet Vision, a mobile and desktop application that has a great user experience,” he says. “We can customize how data appears to meet specific customer needs.”
McNiven adds that CSI Compressco has worked closely with Caterpillar to pull engine panel data and fault codes from Caterpillar’s Product Link™ Elite into its system so it can help customers diagnose engine failures rather than merely informing them one has occurred. The data is stored on Microsoft® Azure. McNiven says Azure’s Event Hub lets customers move data into their internal systems in real time rather than waiting for nightly FTP drops.
At the end of 2020, CSI Compressco had deployed its new IoT gateways across 25% of its compressor fleet to support high-fidelity data transmission and fully enable its digitally enhanced compression solution. The company plans to continue installations at the same pace throughout 2021, reports Matthew Pitcock, its vice president of North American sales for compression services.
“Right now, only a quarter of our fleet has the new hardware,” he says. “Even at this stage, we are seeing opportunities to sit down with customers and analyze the information to improve reliability and operational efficiency. Internally, it is helping us see trends we can use to refine our systems, processes and training programs.”
Managing Field Work
In their work as drilling and completion consultants, Rob Ratchinsky and his colleagues have spent far too much time chasing and writing down data in the field so it could be entered into spreadsheets. “The data was needed for engineers and executives to make the right decisions about their assets, but there had to be a better way to get it to them,” Ratchinsky relates.
Through the ENGAGE platform, operators and service companies can oversee more than 250 kinds of field work. The company says the platform analyzes data from the field alongside historical trends to automatically dispatch drivers and technicians as they are needed, allowing employees to focus on more valuable tasks.
When prices fell in 2014, the team knew drilling and completion jobs would be limited and decided to investigate what it would it take to build an app for oil and gas. “We wanted a platform that could collect data from the field to digitize paper-based processes for requesting, managing and paying for field work,” he outlines. “We ended up creating ENGAGE, which uses machine learning to automatically dispatch services as they are needed.”
To illustrate how the platform works, Ratchinsky points to hauling crude to market, one of the first services it managed. “When ENGAGE predicts that a tank is about to be full, it will automatically dispatch a truck to pick up the oil,” he relates. “For example, it might tell the truck to arrive at 9:25 a.m. tomorrow so it can pick up as much oil as possible, but arrive before the tank gets too full, reducing short loads.”
Through the GPS on the driver’s smart phone or tablet, the platform tracks the truck’s routing and timing, as well as the driver’s movement on site. If the truck picks up the expected volume—say 140 barrels of oil—at or slightly past 9:25 a.m. and drops it off at the expected time, ENGAGE automatically schedules payment to the trucking company for transport and requests payment from the midstream partner. But if something unusual happens, it will flag the transaction for review.
“By automating routine transactions, we can reduce the amount of time the operator’s engineers and back-office staff need to spend reviewing paper or e-mail transactions to catch mistakes,” Ratchinsky details. “For engineers and some executives at smaller companies, that is often a quarter of their day.”
Based on field trials, Ratchinsky estimates that 40% of field tickets contain errors. “There can be as many as 17 human touches between work getting done and the invoice clearing accounting, and with each one, someone might mistype or misread a number,” Ratchinsky explains. “Our platform saves time for both the operator and service provider by eliminating 70% of those steps.”
This means the service company gets paid more quickly and the operator has immediate visibility into its spending, Ratchinsky says.
Ensuring Trust
The platform triggers work and payments by looking at data points the operator and service company have agreed on ahead of time, such as flow volumes for crude oil and produced water hauling jobs. Ratchinsky says it can also schedule repairs based on events such as leaks, as well as preventative maintenance or compliance work based on schedules.
The operator controls what data each service company sees. According to Ratchinsky, both the operator and service company can use the platform to monitor their operations and identify ways to improve. “Over time, shaving 30 minutes here and there can add up,” he assures. “For example, we had a large operator in Utah that was able to complete what previously would have been a year’s worth of workover work by August.
“ENGAGE tracks and approves more than 250 oil field services,” Ratchinsky reports. “On the production side, that includes everything from hot oiling a well to shoveling snow and controlling pests. On the completion side, we help move sand from the mine to the specific frac stage and oversee the logistics associated with water, chemicals and rental equipment. Drilling is similar, with everything from grading the pad to delivering mud and rig fuel.
“We have been able to expand to such a broad scope in part because many of the large companies that use our software have become partners as well as clients,” he continues. “They are investing millions to help us add functionality, which will benefit not only their operations, but also those of much smaller firms.”
The platform’s user base includes independents and private equity-backed firms that only have a few wells, as well as majors such as Chevron, Ratchinsky reports. Most of the users are in the onshore United States, but he says the company is now going live in Canada and plans to expand into international and offshore plays this year.
For other great articles about exploration, drilling, completions and production, subscribe to The American Oil & Gas Reporter and bookmark www.aogr.com.