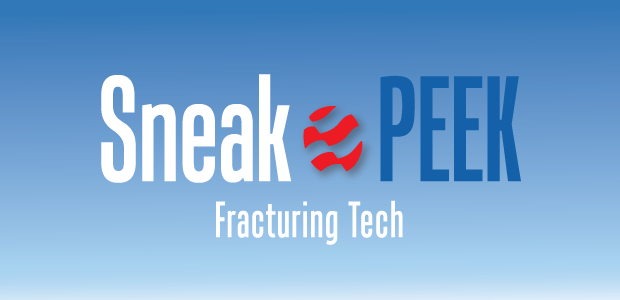
‘Wet Sand’ Offers Multiple Benefits
By Brian Dorfman and Stephen White
DENVER–Proppant usage in hydraulic fracturing operations has changed significantly since the advent of shale plays. In the past 10 years, average proppant demand per well has increased from 1.3 million to 15.1 million pounds, representing an increase of 1,061%. This acceleration of demand has spurred innovation toward lower cost, increased surety of supply and improved well performance.
A brief timeline of the progression begins in the 1970s, when large sand concentrations were pumped using highly viscous (and possibly damaging) gels. The late 1990s were defined by a race for conductivity. Proppant quality became paramount with a movement to manufactured ceramic and bauxite proppants known for their strength, sphericity and smoothness to enhance fracture conductivity. Immediately following that movement was the tight gas boom, which started in the Barnett Shale, where rocks were so impermeable (10s-100s of nanodarcies) that fracture fluids and proppants took a backseat to placement with slickwater–termed “lite” sand fracs.
Eventually, completion designs of the day migrated from tight gas into tight oil plays. Higher frac conductivity came back into style with a movement toward more sand and more viscous fluids. This was accomplished using light gel or viscous friction reducers in very large volumes, with more proppant per lateral foot. Operators’ desire to pump higher volumes of sand in each well resulted in higher well costs in an environment that did not necessarily support those costs. This created a unique problem for forward-thinking suppliers to solve: How do you meet the growing proppant volume demand while controlling the overall cost of the completion?
Ultimately, answering that question led to the discovery of in-basin sand, eliminating the cost of rail and transload handling moves. In addition, miners found ways to reduce the amount of processing that sand undergoes. The increase in proppant consumption per well, along with modern last-mile delivery methods–including hopper bottom trailers and containerized, modular delivery–also has spurred innovation in the method and mode in which frac sand is transported and stored at the well site. The confluence of these innovations in both proppant selection and proppant transportation has led to large cost savings, helping to lower break-even costs across North American unconventional basins.
In-Field Wet Sand
The next evolutionary step in frac sand delivery is now at hand: the combination of in-field mining and wet sand delivery. In-field mining is the progression of in-basin “local mines” to “in-field” or “hyperlocal” mines either in the field where wells are being fractured or less than 15 miles away from active well job sites.
Taken separately, wet sand and in-field mining each provide benefits, but together, they unlock substantially more value for both the sand mine operator and the oil and gas well operator. Wet sand allows for lower capital expenditures when building the mine, as well as lower operating expenditures over time. Wet sand also provides surety of supply at the mine and in delivery to the well site, and drives environmental, safety and governance improvements at both the mine and well site.
The combination of wet sand and in-field mining generates even more benefits, including:
- Locking in sustainable savings by localizing the last-mile supply chain;
- Significantly reducing emissions in frac sand mining and transportation; and
- Reducing employee silica dust exposure at both the mine and well site.
With the emergence of “in-basin” supply over the past five or so years, last-mile logistics quickly displaced rail transportation costs to become the second largest cost component of a well completion. The average well needs 325 truckloads of sand delivered as just-in-time inventory. These truckloads all have to be delivered safely and as efficiently as possible while operating under the following conditions: variable nature of the demand at the well site, limited well site inventory, long transit times, and transit variability (i.e., bad weather, traffic, road closures, load-out congestion).
Frac efficiency has continued to make significant strides. Notable improvements in technology and procedures include improved pump technology, evolution of equipment on the high-pressure side, and the proliferation of simulfrac and superfrac completion designs. These improvements have decreased the number of days necessary to complete a well. This has led to last-mile frac sand providers needing to have more trucks and drivers to safely and efficiently keep pace with the frac job.
The unprecedented surface efficiency increases of a modern fracturing fleet have exposed holes in conventional thinking about sand logistics. The sporadic nature of well site sand demand can cause significant nonproductive time if not balanced in real time. Eliminating the drying process with an in-field mine opens the door to solving numerous operational and logistical challenges of a modern frac job.
Coming out of the pandemic, last-mile companies are struggling to increase trucking resources because of a shortage of truck drivers and increased competition from over-the-road and e-commerce giants. Nonfarm CDL jobs (read “oil field trucking”) were down year-over-year while at the same time, FedEx package deliveries were up 23%. These alternatives offer known, consistent routes, lower maintenance costs and the perk of sleeping at home each night, all of which can be noticeably absent quality-of-life considerations in oil field work.
Case Study Comparison
In-field mining with wet sand offers a solution to this growing operational challenge by reducing the amount of miles traveled, correspondingly reducing the amount of trucks and drivers required to keep a frac job sanded. Consider a case study comparing the last-mile operational differences between running a modern high-throughput fracturing crew from a legacy regional mine 70 miles away from the well site versus an in-field wet sand mine located seven miles away (Figure 1).
Among the key findings is an eye-popping 92% decrease per well in total mileage driven. This equates to a gross mileage reduction of 3.2 million miles annually for an average frac fleet. This reduction in total miles driven can be quantified to a total reduction in carbon dioxide and greenhouse gas emissions of 12,294 metric tons of CO2 saved per year.
Total trucks and drivers required are reduced by 79%. By reducing hauling distance, driver requirements are reduced, simplifying the onboarding, organization and daily coordination of drivers. In turn, this mitigates safety and NPT risks associated with delivering just-in-time inventory. Additionally, last-mile CAPEX requirements are decreased by the reduction in trucks and ancillary equipment.
Moreover, deliveries per driver per day increased 300%. The short-haul drivers averaged 7.2 turns/day with a peak of 10.3, while the long-haul drivers averaged 1.8 turns/day with a peak of 2.2. By reducing hauling distances, truck utilization improves, which allows the truck to make less money per load but more money per day. The container systems’ quick off-load times on location further assist in increasing the truck utilization over competing last-mile delivery systems. Container systems are demonstrably more efficient when run with the proper resource count from short distances. A driver that ultimately can deliver sand for a greater percentage of the day is going to allow the last-mile service to react to the natural swings in demand more effectively.
The number of boxes is reduced by 48%. By reducing hauling length, truck driver requirements and probability of in transit disruptions, the number of assets required both in inventory at the well site and in transit inventory is greatly reduced.
Finally, driver turnover is reduced by a factor of two. By tying the mine’s operation with a frac crew, the stability of the work is increased substantially. By reducing the overall mileage required, the earnings potential for that driver not only goes up, but is repeatable. These two things together help in-field mine hauls compete with over-the-road haul alternative opportunities, an important step to solidifying driver retention.
Structural Problem
Required driver count is a function of daily frac sand consumption range and mileage from origin to destination. The farther the miles and/or the higher or more variable the throughput, the more severe the driver count swings become. This creates a structural problem that directly impacts operational consistency of sand supply to the well site. In order to solve this problem, the ultimate solution is to reduce the overall driver resource needs and increase utilization time per truck.
Figure 2 shows a one-standard deviation “sand throughput day” on the high and low sides. This effectively means that 68% of the pumping days can be expected to fall within this range. As shown, a one-standard deviation event has significantly different last-mile reactions, depending on mileage. On the short haul (seven miles), the range of drivers within that one-standard deviation range in both directions varies from nine to 14 drivers. However, on the long haul, that range fluctuates from 27 to 84 drivers. This variability is what causes cost inflation, driver retention issues and can lead to poor utilization. An in-field wet sand mine addresses this challenge directly and solves the problem definitively.
As shown, when peak sand throughput is hit or the well goes down, the effect on last-mile increases exponentially based on distance from origin to well site. Box systems by design, excel in managing variance in well site throughput, but the reality is that the logistics companies need to make adjustments to their driver counts. Those driver counts must also be constantly rebalanced to account for these swings and solidify an efficient supply chain. The farther the origin is away from the well site, the more difficult and expensive this reaction becomes. If the origin of the product is 10 miles away, driver count swings become significantly less severe. To contrast, a small disruption from 100 miles can swing driver count significantly to keep NPT risk low. Ultimately, the predictability of the driver base and increased utilization per driver in a short-haul environment yields cost savings.
The drying of frac sand and the transportation of that sand to the well site from 65 miles away on a 10,000-ton well emits an estimated 405 metric tons of CO2 into the atmosphere. Running wet sand from a hyperlocal mine emits only ~4% of that number (Figure 3). The combination of eliminating the drying process and reducing miles leads to a substantially reduced operational footprint. This reduction per well is the equivalent of removing 85 passenger cars from the road for a year, or eliminating 975,000 passenger vehicle miles driven in a given year.
Increasingly, a large part of having a sustainable supply chain is addressing GHG emissions in operations. In-field mining and logistics offers reduction in emissions both at the sand mine and during transport from the mine to the well.
Most mines have dryers to dry the sand from 10%-15% moisture to <1% moisture. This is largely a relic of the past when sand had to be shipped long distances by rail, and the need for dryers has been called into question by industry thought leaders given the nature of in-basin and in-field mining and the fact that sand is “re-hydrated” once it gets to the well site. The dryers are the primary driver of energy consumption and per-ton-cost at the mine.
In addition, they account for a significant tranche of the capital required to build legacy facilities. In-field wet sand mining is able to represent large reductions in GHG emissions while saving end-users money on each ton of sand. These emissions benefits are underscored by the large reductions in truck counts with shorter hauls.
Definitive RCS Solution
Wet sand is a definitive solution for employee exposure to silica dust at the mine and the frac site. Respirable crystalline silica dust (RCS) has been identified as an occupational health hazard and is regulated by the Occupational Safety & Health Administration and Mine Safety Health Administration. Beginning this summer, hydraulic fracturing operations must use engineering controls to lower permissible exposure limits of RCS on all well sites to 50 micrograms per cubic meter of air per eight hours (μg/cm/8 hr), with an action limit of 25 μg/cm/8 hr. Moisture in damp sand keeps RCS dust adhered to other particles, reducing hazardous airborne dust in the workplace and surrounding communities.
Numerous silica samples have been taken when running wet sand on personnel and in surrounding areas and were all found to be consistently under the action limit. Eliminating RCS dust also reduces preventive maintenance on frac and sand equipment, and minimizes the need for uncomfortable employee personal protective equipment. In fact, at these levels, the data suggests that dust respirators may not be required, which improves the comfort and vision of on-site personnel (Table 1).
The revolution of the frac sand supply chain has been one of the most innovative subsectors in the unconventional oil and gas space over the past five years. In the Permian, it has contributed to an average $800,000 reduction in total well cost since 2014. The results of frac crew efficiency are forcing another wave of innovation to solve last-mile operational challenges. In-field wet sand mines within or very near to an operator’s acreage solve more than merely simplifying sand processing; they increase frac crew uptime and reduce resource needs while leading to sustainable long-term cost savings in the face of truck driver supply-side inflation pressures.
Unique driver needs are reduced by 79%, average individual driver utilization is increased by a factor of three and variance of driver count to meet the natural swings of sand throughput by the pumping company is reduced significantly. Equally as important is the impact this transition will bring to a reduction in supply chain footprint in the form of reduced CO2 and GHG emissions with resultant ESG benefits. Frac operations using wet sand sourced in the field significantly reduce CO2 emissions.
Moreover, reducing or eliminating the energy-intensive drying process with an in-field wet sand mine helps operators reduce operational NPT risk, simplify the supply chain and minimize needed resources, achieve significant sustainable savings, reduce emissions per well and solve the employee dust exposure problem. It all simply makes too much sense.
BRIAN DORFMAN is vice president of operations at Denver-based PropX LLC, which provides last-mile proppant delivery solutions. Prior to being the first employee and part of the startup team at PropX, Dorfman worked for four years at Halliburton in Colorado and North Dakota. He holds degrees in finance and accounting from Georgetown University.
STEPHEN WHITE is chief operating officer of Hi-Crush Inc. White co-founded Pronghorn and served as Pronghorn’s chief operating officer. After Hi-Crush acquired Pronghorn, he served as vice president of logistics and field services at Hi-Crush. Prior to Pronghorn, White was director of business operations at Rockpile Energy Services.
For other great articles about exploration, drilling, completions and production, subscribe to The American Oil & Gas Reporter and bookmark www.aogr.com.