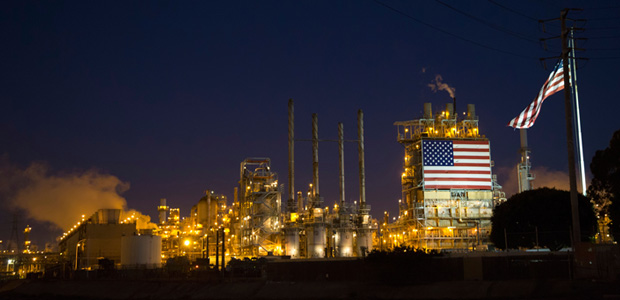
Refining
Catalysts Optimize Tight Oil Refining
By Mary Jo Wier, Dan Sioui and Steve Metro
DES PLAINES, IL.–Domestic oil production from shale plays continues to displace imports, which declined by about 40 percent between 2010 and 2013. Domestic crudes offer lower-cost raw materials and supply surety to U.S. refineries, but also present new technical and logistical challenges.
Refineries face the same general business pressures as companies in the upstream and midstream segments: ever-increasing demands to optimize existing assets and improve operating efficiencies in order to maximize profitability regardless of crude oil and refined product prices. The critical step in increasing profitability is to properly define refining objectives and constraints, and then leverage appropriate process technologies to optimize a refining configuration by capitalizing on the increasing supplies of production from tight oil plays.
The light, sweet crude oil characteristic of tight oil plays is contrasted with the heavy, sour Canadian tar sands bitumen. These crudes have very different yield patterns for refined products, as well as contaminant levels, impacting refiners’ processing units and product slates. Tight oil crudes typically have higher light and heavy naphtha yields, presenting increasing challenges to the naphtha complex, typically consisting of naphtha hydrotreating (NHT), light naphtha isomerization and catalyst regeneration platforming units.
The lower vacuum gas oil (VGO) and vacuum residue yields directionally decreases coker, fluidized-bed catalytic cracker (FCC) and alkylation rates, decreasing their contribution to the gasoline pool. Conversely, light naphtha, isomerate and reformate octane-barrels increase in the gasoline pool and play an increasing role in gasoline production and profitability.
Each refinery has a unique configuration, set of processing objectives, equipment limitations, and budget constraints. Therefore, there is no universal solution to maximize profitability. Solutions for refiners located in the Gulf Coast and Midwest regions that can access and sell products more readily may differ from refiners in other regions who incur higher product transportation costs.
Tight Oil Yields
The crude assay reflects the yield pattern and is key information for determining the refinery products. Figure 1 is a plot of the yield by weight percentage of LPG, naphtha, kerosene, diesel, vacuum gas oil and vacuum residue for several crudes with varying API gravities. The tight oil crudes (Bakken, Eagle Ford, Utica, etc.) are typically lighter with higher API gravities, and have predominantly higher LPG, naphtha with less heavy VGO and vacuum residue materials. Conversely, Western Canadian Select (WCS) is a blend of oil sands. However, even after blending to an API gravity of 20-21 degrees to increase flow properties, WCS is still viscous, making it challenging to transport.
A crude oil’s gravity can be used to approximate key properties, such as yields, contaminants and paraffin concentration. There is a general trend of increasing lighter hydrocarbons with increasing API. Consequently, Eagle Ford oil with an API of 55.6 degrees has a higher naphtha yield than Bakken oil with an API of 42.3 degrees.
Contaminant levels also trend with gravity. For example, sulfur and nitrogen concentrations are generally lower for the sweet, lighter crudes produced from tight oil plays and higher for lower-gravity crudes such as WCS. However, higher-API gravity crudes typically have higher paraffin (wax) and naphtha concentrations.
These trends are applicable within individual cuts. For example, tight oil diesel and naphtha cuts are more paraffinic, with low contaminants. WCS diesel cut is lower in paraffins, resulting in diesel with improved cold flow properties, but lower cetane.
Processing Tight Oil
A refinery linear program (LP) was developed to evaluate the impact of changing the crude slate from a conventional mix of waterborne imports to domestic tight oil and WCS crudes. The modeled refinery configuration included a coker, VGO hydrotreater, FCC, HF alkylation, naphtha hydrotreater, isomerization and CCR platforming unit (Figure 2). The LP assumes a crude processing capacity of 150,000 barrels a day with of a mixture of Arab Medium, Maya, and WTI crudes.
The price basis used in the study included transportation fuel specifications based on typical U.S. product requirements, including for ultra-low sulfur diesel (ULSD), RBOB gasoline, naphtha, butane, propane and bunker fuel oil. Table 1 shows the crude properties used in the study.
The key LP findings when processing higher-gravity oil from tight oil plays include:
- Crude price is the key economic driver;
- Increasing API gravities results in higher light naphtha (C5/C6) yields, which impacts the isomerization unit (NHT and CCR platforming unit rates also increase, but at a lower percentage);
- Decreased diesel production as a result of less upgrade of vacuum residue material (the diesel has higher cetane with poorer cold flow properties);
- Isomerate and reformate octane-barrels increase in the gasoline pool while FCC naphtha and alkylate decrease (gasoline pool barrels can decrease if the decrease in FCC naphtha plus alkylate is greater than the increase in isomerate and reformate in the pool); and
- If excess light naphtha is sold, the price differential between the cost of the crude and the selling price of naphtha determines profitability.
Balancing light, sweet crudes from tight oil plays with heavy WCS is important to maximize current domestic refining assets. In fact, processing unblended tight oil can actually be unprofitable for refineries. A possible scenario would be if light naphtha cannot be blended into the gasoline pool because of either due process unit constraints or gasoline pool Reid vapor pressure (RVP) limits, resulting in excess naphtha being sold.
The key to profitability is optimizing the naphtha complex. Figure 3 shows a block flow diagram of a naphtha complex, including a naphtha hydrotreater, naphtha splitter, isomerization unit, and a UOP Continuous Catalyst Regeneration (CCR™) platforming unit. The flow rate to the naphtha complex typically increases as the crude becomes lighter. Because the isomerate and reformate blend stocks are a larger percentage of the overall gasoline pool, optimizing these assets is critical to maximizing refining economics.
Vacuum residue can be processed in a coker unit to produce naphtha, which is then further hydrotreated in an NHT unit. Common process concerns are metals, olefins, sulfur, nitrogen and silicon from antifoam used in coker drums. The higher level of contaminants and additional coker naphtha to the NHT results in more severe operating conditions, impacting reactor pressure, LHSV (volume of feed in cubic meters per hour) and hydrogen gas consumption. Therefore, attention to the NHT and operating conditions should be re-evaluated when processing heavier bitumen crudes.
Catalyst Improvements
Processing tight oil shale crudes such as Bakken, Utica and Eagle Ford, coupled with heavy Canadian bitumens, provides significant margin opportunities, but it also presents new challenges. With higher light naphtha yields, optimizing the naphtha complex is a key component to profitability. Existing refinery configurations can be optimized to process a new crude diet consisting of tight oils to increase profitability.
Profitability can be increased further when employing the latest high-yield catalysts. Catalyst improvements–including a new cobalt molybdenum hydrotreating catalysts for straight runs and low nitrogen feeds, and a robust catalyst for use in naphtha hydrotreating applications to remove sulfur and nitrogen compounds with cracked stocks and high nitrogen feeds–are enabling refiners to optimize the NHT unit and increase feed rate and/or reduce utilities.
The catalyst for cracked stocks and high nitrogen feeds was evaluated for a plant with the option to run either a 75-percent Bakken/25-percent WCS blend or a 75-percent Eagle Ford/25-percent WCS blend. By applying the new-generation catalyst, the feed rate increased by 16 and 49 percent, respectively, compared to the base case.
The economic advantages of higher refining activity, lower fill costs and reduced fuel costs associated with the advanced naptha hydrotreating catalyst would save more than $1.36 million over the cycle life of the catalyst on a 40,000 bbl/d NHT unit. The longer catalyst life can provide additional benefits and cost savings by extending shutdowns between skimming, replacing and/or regenerating.
In addition, evaluating the example plant shows more than $8 million would be generated annually using an advanced CCR platforming catalyst on a 30,000 bbl/d CCR unit at ~101 research octane number clear (RONC). Moreover, $4 million would be obtained annually with a high-activity isomerization catalyst running a 75-percent Eagle Ford/25-percent WCS blend. The higher isomerate octane-barrels would allow the CCR platforming unit to operate at lower severity, resulting in higher product values.
The development of unconventional tight oil plays is a game-changer for North American refineries. However, along with new opportunities for processing light tight oil crudes blended with heavy Canadian bitumen come new challenges to refiners. Technology advances such as new-generation catalysts and process designs can assist refiners in optimizing existing and new facilities to take advantage of growing North American oil production.
Editor’s Note: The co-authors acknowledge UOP colleagues Alex Sabitov, Mark Lapinski, Ka Lok and Soumendra Banerjee for their technical input and assistance. More detailed information on optimizing naphtha complexes to accommodate supplies from tight oil plays is available in a technical paper the co-authors presented at the American Fuel & Petrochemical Manufacturers’ 2014 annual meeting.
MARY JO WIER is an engineering and scientist principal in research and development at UOP LLC, a Honeywell Company, in Des Plaines, Il. Her background includes isomerization, platforming process development and refinery technology integration evaluations. Wier holds a B.S in chemical engineering from the Colorado School of Mines.
DAN SIOUI is manager for strategic marketing for refining at UOP LLC, a Honeywell Company. He has more than 20 years of experience in the refining industry, and holds engineering degrees from Worcester Polytechnic Institute and the University of Massachusetts at Amherst, and an M.B.A. from the University of Chicago.
STEVE METRO is senior business leader responsible for UOP’s naphtha product department. Other roles include catalyst product management, and equipment and process development. Metro holds a bachelor’s in chemistry from Northeastern Illinois University, and an M.B.A. from Northwestern University.
For other great articles about exploration, drilling, completions and production, subscribe to The American Oil & Gas Reporter and bookmark www.aogr.com.