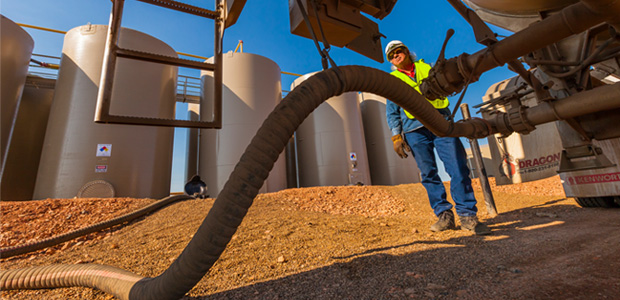
Production Measurement
Gauging Accuracy Key In Resource Plays
By Jim Gardner
FOOTHILL RANCH, CA.–The scope of operations in unconventional resource plays has changed the oil and gas industry in many ways, including the fact that producers are now dealing with larger volumes of oil and liquids on their production locations. In the past, small measurement errors were not uncommon, and were even considered acceptable in many cases when dealing with relatively small volumes of produced liquids on single-well pads. However, the high initial rates achieved by horizontal wells and the utilization of multiwell pads have increased the daily volumes of oil and liquids being measured and transferred from a single pad location to several thousand barrels per day.
Accurate measurement is critical in generating full potential revenue, especially during periods of depressed commodity prices. Oil and gas companies must be sure they are being paid accurately for their oil production, and with advances in automation, they also want to know both inventory and custody transfer events (sales) in real time. Accurate tank level measurement is essential. A measurement error as small as 0.02 percent at a central facility transferring 10,000 barrels a day would equate to the loss of $100 a day at an oil price of $50/bbl, or $36,500 annually.
In addition to precise level measurement, temperature accuracy also is critical. An error of 2.5 degrees Fahrenheit on a 20-foot production tank is the equivalent of a ¼-inch level error. If the producer is moving multiple tank loads each day, even relatively small temperature errors can again cost hundreds of dollars a day in potential revenue losses per tank. When the losses are totaled across an operation, they can potentially represent hundreds of thousands of dollars in annual lost revenues for the producer.
Considering that the average production tank holds 2.6 barrels per inch, the case for extremely accurate level and temperature measurement on any high-volume production tank is readily apparent. The good news for producers is that measurement errors can be eliminated by equipping tanks with systems that ensure highly accurate measurement. In fact, today’s state-of-the-art measurement equipment can achieve accuracies of ±0.25 percent, which is equivalent to measurement accuracies of 399-401 barrels for every 400 barrels sold.
Automatic Tank Gauging
The multiphase flow characteristics of many unconventional resource plays make accurate gauging more challenging, with wells often producing some percentage of oil, water, condensates and natural gas components. A gauger’s task is to determine both the quality and quantity of crude oil in a tank by sampling the oil, checking the gravity, looking for sediments, recording the temperature, and measuring the volume. Tank gauging is an essential element of inventory control, custody transfer and leak detection.
In the late 1990s, automatic tank gauging technology began replacing manual tape gauge methods. There now are many types of automated systems available, each with advantages and disadvantages. Instrumentation manufacturers have learned that building a device that can produce accurate, repeatable measurement of crude oil in production tanks is one of the most challenging endeavors in the business. Crude tanks can gum up and spit out new technologies as fast as they are introduced. Oil viscosity can change from field to field and even pad to pad, drastically impacting measurement accuracy.
In addition, many wells produce corrosive gases that can destroy gauges in a matter of weeks. Consequently, equipment manufacturers are constantly balancing accuracy with robust reliability to provide products that can work in all the harsh and varied conditions inherent in the oil field. Many automatic tank gauges will work in multiple environments, and manufacturers often make multiple types of gauges using different technologies. Each type has a “best fit” application, but also has limitations in some environments.
TABLE 1
Types of Automatic Oil Measurement Systems
*Pressure gauges cannot determine the difference between oil and water
**Ultrasonic gauges cannot determine the difference between oil and water
***Wave-guided eadar can detect differences between oil and water, but may struggle with emulsion and interface accuracy
For example, ultrasonic devices are ideal for applications with clean water. In hydrocarbon environments, however, the lens that emits and receives the ultrasonic signal periodically becomes coated with a hydrocarbon film, which reduces measurement accuracy and will eventually make the device unreliable. Ultrasonic gauges also do not provide any temperature measurement. Like any tool, ultrasonic works great when used in the right application, but crude oil tanks are generally not a good fit.
Pressure gauges are often positioned at the bottom of an oil tank to measure the foot pounds of pressure the liquid is exerting (i.e., the weight of fluid in the tank). There are two problems with this approach. The first is distinguishing what type of liquid is in the tank, and how much of it is oil and how much is water. All crude oil tanks will have some water captured in the tank, even after separation. Pressure gauges cannot tell water from oil. Second, pressure gauges are analog devices that can be affected by temperature cycles or gas pressure building up in the tank as it heats or cools. Pressure gauges also do not provide temperature measurements.
Guided-wave radar gauges were first designed for refined products and provide excellent top gauge readings that are accurate and repeatable. However, results vary in crude oil applications. Wave-guided radar relies on a cable to guide the radar beam from the instrument to the bottom of the tank. In high paraffin environments, some operators have found that paraffin collects on the cable and adversely impacts the accuracy of the readings. Another issue is that the cable is made of a metal that is susceptible to corrosion in production environments with hydrogen sulfide, which also can also degrade the accuracy of readings. In addition, radar gauges do not provide temperature measurements.
Temperature Measurement
Both magnetostrictive and resistive/reed switch gauges measure temperature in addition to tank levels. Magnetostrictive gauges can detect both the top level and the interface level to 1/10 of an inch, and have very good repeatability. The gauge is run into the tank through a port next to the thief hatch and has two floats that are weighted for the specific gravity of the liquids (one for water and one for oil). Most magnetostrictive gauges have high power draw, which can adversely affect the life on battery-powered wireless nodes.
Magnetostrictive gauges are available in both rigid and flexible models. The rigid models can be extremely difficult to install on production tanks. If the tank is 20 feet tall, the sensor must be 20 feet long and must be raised 20 feet above the tank before it can be lowered into place. This commonly requires a crane or a bucket truck for installation, not to mention the logistics of transporting it to location. The flexible models can be coiled and installed by one technician. One challenge is that in volatile tanks with high turbidity, the flexible gauge can be difficult to keep from swinging inside the tank.
Most magnetostrictive sensors also have a temperature transducer in the probe to provide both volume and temperature liquid measurements for custody transfer. However, magnetostrictive gauges may not be suitable for tanks with higher-temperatures liquids (in excess of 150 degrees).
Resistive gauges use a series of reed switches in a probe that are activated by magnets in the two floats on the outside of the probe. The two floats are again weighted to the specific gravities of oil and water, so the gauges provide extremely accurate and repeatable measurement for both oil and interface levels. Power draw is very low and battery life can be seven to 10 years on a wireless node.
Resistive sensors can be purchased in either a rigid model or in a flexible model. The rigid design is better in high turbidity conditions, but as with magnetostrictive systems, it is difficult to install without a crane or bucket truck. The flexible model is easy to install. One technician can install a probe in a tank in 15 minutes with a wireless version. In tanks with high turbidity, a stilling well around the gauge is optimal to ensure accuracy and prevent potential damage to the gauge. Resistive gauges provide oil and water level measurement and temperature for the liquid being measured, and are available for applications with temperatures as high as 248 degrees.
Today’s sophisticated tank gauging technologies can measure levels for two liquids to within a 1/8-inch accuracy over the height of any tank and provide temperature measurements to allow crude oil sellers and buyers to reconcile volumes based on temperature. As noted, even seemingly small errors in tank level and temperature measurements can add up to significant revenue losses across a field operation.
With horizontal drilling and multistage fracturing changing the volumes of liquids produced on each tank location, the need for accurate measurement has become a critical success factor for both crude oil producers and purchasers. When considering the best fit for a given application, the operator must understand the plusses and minuses of each measurement solution available and the characteristics of the field. Special consideration should be given to oil temperatures above 150 degrees, how much volume is going into the tank, and where the fill line is in relationship to the gauge. As with any equipment purchase, working with a qualified factory-trained distributor is crucial to the overall success of an installation.
JIM GARDNER is a regional vice president at OleumTech Corporation. He has worked in the oil and gas industry since 1975. Before joining the company, Gardner served for 12 years as oil and gas industry manager at FreeWave Technologies Inc. Prior to that, he had served as a regional manager at AMF Tuboscope, senior vice president and general manager at Remote Operating Systems, and product manager at ABB Totalflow. Gardner holds a bachelor’s from the University of Washington.
For other great articles about exploration, drilling, completions and production, subscribe to The American Oil & Gas Reporter and bookmark www.aogr.com.