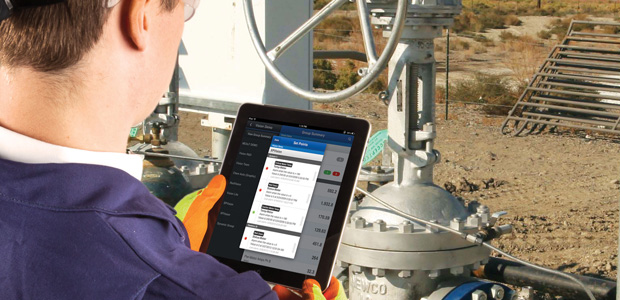
Production Engineering
Mobile App Simplifies Production Monitoring
By Sven Haberer
HOUSTON–In today’s oil field work environment, production engineers have limited desk time to accomplish their daily tasks. At the same time, they are being required to fit more responsibilities and work activities into each day. The use of mobile work applications promises a practical and timely solution to these challenges.
If implemented correctly, mobile applications enable their users to be more productive while away from the traditional office location. For the production engineer, this translates to an ability to remotely monitor well conditions to reduce downtime and maximize production.
Whether an onshore unconventional field development project or an offshore asset, remote monitoring enables oil and gas companies to optimize production operations and attain a high level of equipment dependability from production sites. However, one key to realizing the potential of remote monitoring is ensuring that production engineers have quick and reliable access to production data and notifications of events or alarm conditions.
These needs have been addressed through the development of a mobile application that allows production engineers to securely access well data through the app using smart phones or tablets running Apple’s iOS™ operating system. A touch-friendly Web version has also been developed to enhance the user experience for hypertext markup language (HTML5) mobile devices.
Figure 1 shows sample screen captures of pump data from the mobile app as displayed on a smart phone. The available features do not only include real-time data access and alarming, but they also allow interaction using manual data entry, memos, the ability to request a demand-scan to receive the latest real-time data, and the ability to issue two-way control commands form the mobile device to the field controller.
The mobile application is an extension of a Web-enabled monitoring solution originally designed for use on desktop computers. This solution, in conjunction with advanced electric submersible pumping (ESP) systems, is currently optimizing the production of more than 2,500 wells worldwide in both conventional and unconventional plays. Engineers and technicians from West Texas to Africa are accessing real-time well data anytime, anywhere on a secure Internet connection using mobile application connectivity.
Extended Flexibility
Mobile applications extend the flexibility of the monitoring solution, by giving users the flexibility to monitor their wells 24 hours a day, seven days a week without being confined to their desks. This allows production engineers to be more efficient and to extend their productive hours and overall efficiency. The ability for real-time data access also means that wells and equipment are no longer at risk simply because the engineer is not sitting at a desk in the office.
Access and security permissions are mirrored directly from the user’s access and security permissions. Just as in the desktop version, the application enables data to be viewed at group, well and tag levels. Alarms can be quickly visualized and acknowledged directly within the mobile application. The user can also disable alarms to avoid “nuisance trips” during known alarm periods.
Memos can be entered within both the mobile application and the standard Web interface, which enables knowledge sharing on known issues and changes to the device within the program by other users. Manual entry allows field data, such as tank levels, to be entered directly into the system’s central database. Both memos and data are available in offline mode when the engineer has no Internet access or is in a field location with poor connectivity. The memos and data entered while offline are then synced back to the central database once connectivity is restored.
The database is updated immediately, giving other users access to the most recent field data, wherever they might be located. This feature improves the efficiency and response of the field maintenance crews, who can then focus their work on only those wells that have triggered an alarm that indicates an operational problem.
The mobile application is highly intuitive and can be learned in minutes. Typical mobile device gestures such as tap, swipe, flick, touch and hold are supported within the application. Search and filtering functionality ensure fast access to relevant data. Ultimately, the mobile version allows the end user to perform nearly all functions available in the full Web-based platform, but with the added flexibility of “on-the-go” access.
Case Study
An independent operator in Southeast Texas needed a more efficient and proactive approach to manage its wells while engineers were working away from the traditional office setting. Most of the information gathered from the wells was communicated and updated to the server in real time, but the operator chose to use manual gauges to gather the tubing and casing pressures. This resulted in daily trips to each well site to manually collect the pressure data, and an additional data entry step at the office to upload information to the server through the Web interface. This lapse of time between recording the data at the well site and actually entering it into the database back in the office was delaying the availability of the most current well information.
While in the field, the technicians were also comparing the most current ESP data onsite with the latest physical data reports from the office to help identify changing parameters and potential maintenance issues. Without real-time access to the latest information, the technicians had to visit every single well without discretion, which limited the number of sites they could reach on any given day.
The operator decided to transition to the mobile application to help streamline this process and enable real-time access, monitoring and control. The company’s field technicians began using the application on their mobile devices to actively monitor well parameters and receive notifications while in the field.
Access to the real-time well information allowed the technicians to proactively address problematic wells based on live information, rather than visiting each well to determine the status. Performance criteria and alerts set by the operator helped them operate by exception while in the field, and focus only on the wells that needed attention. This improved process allowed the technicians to work more efficiently and reduced overall travel time by more than 40 percent.
The technicians also began using their mobile devices to enter the casing and tubing pressures while at the well sites. As soon as the values were entered, they were instantly uploaded to the database platform, allowing any engineer or field technician with access to the system to view the most current well information in real time from their own mobile devices.
As noted, in remote field areas without connectivity, an offline mode allows the technicians to enter the data, which are then automatically synced with the platform as soon as connectivity is restored. Using the mobile application has eliminated the need for redundant data entry at the office and ultimately has reduced data entry errors by 30 percent.
For this operator, user adoption and use of the mobile application grew by 52 percent within only one month. In addition to significantly increasing the efficiency of field visits, the mobile application helped improve the overall integrity of the well information recorded by the technicians. Because of the process improvements and flexibility gained, the operator now prefers to use the mobile version to view well data and remotely control its wells.
The first-generation mobile app, while an important step forward in giving users access to real-time well data wherever they might be, is still limited in that it only provides the raw numbers without a historical context. Next-generation solutions are planned that will provide the data in a graphical format to understand production trends over time. The ability to see historic trends in well data is a powerful addition to the technology’s capability, giving the user a better intuitive understanding of how performance at the well head is changing and allowing faster decisions to be made to correct problems.
SVEN HABERER is the product line manager for production decision services at Baker Hughes in Houston. He has extensive experience in production monitoring, artificial lift, remote services, drilling and field data acquisition. During his 18-year career at Baker Hughes, Haberer has held roles as a real-time service manager, field test engineer, system integrations engineer, and software engineer. He holds an M.S. in mechanical engineering from the Karlsruhe Institute of Technology in Germany.
For other great articles about exploration, drilling, completions and production, subscribe to The American Oil & Gas Reporter and bookmark www.aogr.com.