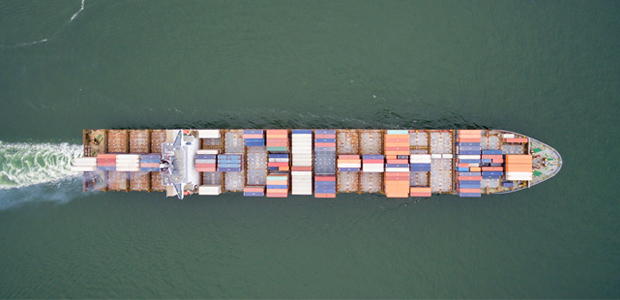
Asset Management
Offshore Operators Have Tools To Reduce Risks, Improve Logistics
By Robert Kessler
Oil rigs and other fixed offshore assets face many threats in the marine environment, including allisions when vessels collide with stationary objects and unexpected equipment failure, as well as health, safety, and environmental hazards.
These and other risks can be mitigated by identifying and prioritizing operational risks at each site and understanding their financial impacts, and by applying smarter ways to manage and optimize the performance of widely dispersed assets in harsh and hard-to-monitor offshore environments. Risks are mitigated further by using unmanned aerial vehicles to conduct inspections in hard-to-reach areas. These take people out of harm’s way while moving the oil and gas industry closer to fulfilling its vision of the autonomous rig.
According to the Bureau of Safety and Environmental Enforcement’s 2016 annual report, nine collisions, inclusive of vessel allisions with fixed assets, were reported in the U.S. Outer Continental Shelf during the fiscal year. Over the 10-year time frame considered in the report, an average of 17 collisions a year were reported, just under 13 of which were defined as major collisions resulting in property or equipment damage greater than $25,000.
Numerous factors influence the risks that vessels pose to fixed offshore assets, including regional security concerns, weather patterns, sea conditions, local shipping lanes, and nearby rig traffic. Operators typically set a radar “guard ring” and associated alerting mechanisms to provide notification when vessels draw within a set distance from an asset.
Unfortunately, an often high volume of false radar alarms from the asset’s own support vessels typically desensitizes watch teams. Plus, there is no way to know the approaching vessel’s speed. Setting a guard ring large enough to account for fast-approaching vessels often overwhelms watch standers with false alarms, while too small a ring doesn’t allow adequate mitigation notice.
Many operators are solving this problem through a traditional combination of vessel Automatic Identification System (AIS) data, radar, and other data inputs to detect, assess and mitigate vessel risks, using solutions that must be deployed onboard each asset. Others are using a more collaborative, Web-based system that facilitates centralized risk monitoring, provides analytical reporting tools and access to historical data, and enables operators to configure and issue automated alerts based on predetermined parameters associated with each asset’s unique risk profiles.
Today’s tools ingest required global positioning system positions from AIS transmitters, radar targets, and other sensors, and integrate with satellite AIS for a complete offshore picture. They often are augmented by shore-based monitoring services providing a 24/7 “virtual watch team” for assessing asset threats anywhere in the world. Disparate data sets are aggregated and transported to shore to deliver centralized visualization and actionable intelligence, giving watch teams everything needed to know about a vessel, a point of interest, or a user-defined zone. The solutions filter out false-negative alarms so that alerts only pertain to vessel interactions with identified assets.
Operators can use this information, along with historical data about vessel movements and triggered alerts, to optimize operational efficiency and emergency response while facilitating the ongoing establishment and disciplined reporting of key performance indicators. They can target specific fleets or individual vessels for outreach and education, and focus special attention on those that appear to trigger alerts consistently or fail to comply or communicate with the asset watch team. Operators also gain better insights into how to define procedures for consistently assessing all threats and associated mitigating steps, and for properly training staff to validate risks and initiate mitigation.
These same risk-mitigation concepts also can be extended beyond vessels to other asset risks, including those posed by unexpected equipment failures.
Reducing Risks
Offshore equipment failures can be difficult to predict, as they often are attributed to multiple interrelated root causes. Smarter methods can be used to manage and optimize the performance of widely dispersed assets deployed in harsh and hard-to-monitor offshore locations. The goal is to improve operations across a multitude of assets and processes over the life of the oil field, from exploration to decommissioning, at lower costs while decreasing downtime, improving safety, and reducing energy consumption.
These goals can be accomplished with an asset performance management (APM) platform, which enables operators to predict and prevent equipment issues before they occur; improve compliance and integrity management through improved risk monitoring and mitigation; and optimize asset usage and uptime through better insights about equipment health, availability, reliability, failure modes, life-cycle costs, and other parameters.
APM solutions must be capable of transporting, storing, accessing, organizing, and sharing large volumes of information, bringing that into a single visualization dashboard, and generating actionable analytics and alerting. Data integrity must be ensured from all endpoints across the network infrastructure and back to the corporate office, throughout the oil field life cycle. This requires offshore operational experience, an end-to-end perspective across the system infrastructure, and the ability to solve numerous technical challenges.
Operators must tailor remote sensing solutions to specific requirements for monitoring vessels, rigs and subsea assets. All sensor data, regardless of source or protocol, must be brought into a single aggregated view that can be shared for comparative analysis. Those data sources include well control, communications and mud-loss sensors to those delivering temperature and pressure inputs from compressor systems. The APM system must support all protocols, from object linking and embedding for process control, to serial and ethernet Modbus communications protocols and the BACnet protocol, using various protocol interpreters.
The APM solution also must support video archiving and searchable/indexed retrieval, and handle petabytes of high-bandwidth video data from applications including CCTV surveillance, instrument monitoring, photogrammetry services, and digital point cloud data used for remote piloting. Live, high-volume video streaming is increasingly commonplace–as an example, Oceaneering typically carries between 200 and 250 live subsea video feeds simultaneously from its remotely operated vehicles.
There already are bandwidth challenges at these feed volumes, and challenges will intensify as video files move beyond standard-definition to high-definition formats, especially with the transition to augmented-reality capabilities that enable operators to pilot ROVs from a shore-side location as though they were there, using 3-D imagery to control robotic arms and pull umbilicals in real time.
The next APM challenge is how to connect the sensor, video and other data sources to either a shore-side data center or a cloud-based solution. In either case, it is necessary to have both offshore and onshore points of data aggregation, using networking solutions that are reliable, responsive and secure, and with ample processing, bandwidth, and storage/retrieval capabilities. Real-time data solutions provide common and scalable ways to link rigs, platforms, and vessels with global operation centers, and to backhaul sensor data (including live video).
Finally, APM solutions require easy-to-use dashboards or other visualization solutions for a consistent user interface that optimizes collaboration. Also important are robust and flexible alerting capabilities, and a “big data” strategy for turning operational data into tangible business value.
Solutions should facilitate the full range of continuous real-time analytics with a path to self-learning, risk-based predictive models. They also must maximize uptime and pre-empt unexpected equipment outages by managing a reliable set of alert-state windows in the event of anomalies, and prompting users to execute optimal maintenance policies and protocols for the top issues demanding assessment and action. This requires an understanding of what is most important during each life-cycle phase across the entire asset infrastructure.
Cutting HSE Risks
UAVs reduce risk by performing hard-to-reach inspections without exposing personnel. They also improve data acquisition speed and quality, and can be used to enhance security, emergency response, and environmental and regulatory compliance. Imaging and sensor payloads might include HD video equipment, high-resolution still cameras, thermal imaging cameras and emission sensors, as well as light detection and ranging (LiDAR) laser scanners for creating point clouds and digital elevation models between the sea surface and seafloor.
The value of UAV programs is maximized when they are an integral part of an operator’s risk mitigation platform with comprehensive video management and shore-side remote monitoring capabilities. They eliminate the hazards of rope-access inspections in the offshore environment, while circumventing the many limitations of alternative data collection methods. Some organizations have augmented their UAV programs with robotics technology, combining magnetic crawlers with unmanned aerial system (UAS) technology so they can aggregate and organize inspection data and imagery from multiple sources to streamline and improve the detection of corrosion, cracks, or other infrastructure maintenance issues.
Safety is paramount for every application of UAS technology. The International Association of Oil & Gas Producers (IOGP) released its UAS guidelines, in addition to its Aircraft Management Guidelines (AMG), to provide a framework of guidance and expectations for UAS operations. In addition, the IOGP’s S6 appendix to the AMG delivers the latest recommended guidance for safe, effective, and efficient management of all aviation operations. It defines minimum requirements for safety management systems, quality assurance and emergency response planning.
Offshore asset operators must anticipate and pre-empt numerous threats from vessels, unexpected equipment malfunctions, and HSE hazards. Centralized monitoring platforms simplify these tasks, while providing holistic views, actionable analytics, and flexible alerting capabilities. As these solutions, along with UAV programs and other technologies that protect workers from dangerous situations while improving data acquisition, become more common, the industry will move closer to realizing the benefits of increasingly autonomous rigs featuring comprehensive self-monitoring and predictive risk-mitigation capabilities.
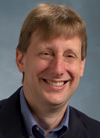
ROBERT KESSLER is the program manager, maritime global data solutions, for Oceaneering International Inc. Prior to joining Oceaneering, he was director of business development enterprise software at PortVision in Houston, moving over from the same position with ASIRSIS. Kessler is a 1988 graduate of the U.S. Merchant Marine Academy.
For other great articles about exploration, drilling, completions and production, subscribe to The American Oil & Gas Reporter and bookmark www.aogr.com.