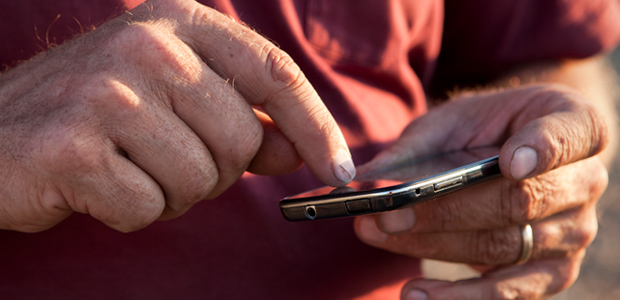
Upstream Digital Solutions
Real-Time Collaboration Breeds Cost Efficiency
By Chase Feiger, Ryan Junee, Lawrence Whittle and Ken Pulverman
SAN FRANCISCO–A well site holds a stunning array of high-tech equipment that gathers data from drilling, completion, and production operations. However, on most field locations, workers still make handwritten notes on paper and attempt to follow operational procedures in hard copy books or binders that typically are not near the job site. Following the lead of other industries, the technology now exists to enable digital, collaborative work among supervisors, engineers, field technicians, suppliers, etc., in oil and gas operations.
The opportunity is clear. An estimated 13 percent reduction in accidents and injuries can be achieved in the next decade by connecting workers digitally, according to a recent World Economic Forum publication. Productivity for these same workers could increase by up to 15 percent by 2025, and the World Economic Forum predicts another 6 percent reduction in accidents and injuries from further automation and standardization. Industry 4.0, the drive to seamlessly integrate human and machine work into unified business processes, is further accelerating these advances.
The cost of business as usual also is clear. Industry estimates indicate that nonproductive time accounts for up to 32 percent of deepwater drilling costs. This represents billions of dollars of unnecessary and unproductive capital spending each year worldwide. A simple maintenance error can lead to a $2 million operation to pull a blowout preventer or require two days of rig time to trip pipe. Procedural mistakes are not only expensive, but can result in increased health, safety, and environmental risk exposure.
Other industries are recognizing the need to drive out variability and standardize operations to ensure a predictable outcome and establish a clear baseline for improvement. As the drive to deploy an Industry 4.0 strategy extends to all industries, oil and gas companies are coming to the same conclusion and are beginning to deploy key technologies to support consistent processes across operations and disciplines.
Examples from other industries abound. The computer chips that power electronic devices are manufactured in high volumes in locations around the world. Chip manufacturers have adopted stringent requirements for all processes to achieve a reliable output with a finished product that produces consistent and predictable performance. Electronics are very small, leaving no margin for error. Every input, pathway, and operating condition is copied precisely. Intel’s vice president of manufacturing once explained the approach this way, “We are not smart enough to know what matters and what does not, so we copy everything.”
In aviation, millions of customers' lives are at stake every day. Maintenance and onboard crews must never skip ahead on their checklists, even if it means a late gate departure. The consequence of nonadherence is too severe. More than a dozen crashes between 2005 and 2015 involved airline or commercial charter plane crew members failing to follow established procedures. The drive to standardize work processes thus never stops.
In healthcare, patient safety always has been a concern. Digital charts have helped standardize and document care. When collaboration tools were added, care givers were enabled to work together effectively and patient safety saw a steep uptick. It has been well documented in medical environments that the simple enforcement of team-based work processes can dramatically reduce patient complications. Digitization and collaboration are both necessary ingredients.
Real-Time Collaboration
So what do lessons learned in standardizing work processes in chip manufacturing, aviation and healthcare have to do with the oil and gas industry? With thousands of maintainable assets under management and billions invested in drilling and production operations, operators have a big stake in making sure things are done right the first time. A great deal of work has been done to gather data on conditions downhole, at the rig and in the field. Work is underway to fully capitalize on all those data through predictive systems and automated control.
The overlooked opportunity lies in digitizing in real time the output of human work. By connecting decision makers and field workers, suppliers and engineers, real-time collaboration and control is enabled and everything is recorded for analysis. To achieve this goal, technology must be employed that also ensures that any work is supported by accurate and complete information. This information has to be easily accessible anywhere on any device and there can be no room for misinterpretation. This transformation to digital enablement often comes in the form of a procedure, standard operating procedure, or a complete business process that may include video and images to speed understanding of individual actions.
Collaboration is a necessary companion to digitization. Most work performed in oil and gas companies is collaborative. Having a tool that enables immediate and effective collaboration both within and external to an organization helps ensure that decisions are made with transparency and complete information, and are understood by all stakeholders and team members.
Generally, three major factors contribute to noncompliance to predefined procedures and processes. The first is a lack of knowledge or skills. Whether because of the “great crew change,” manpower constraints, unexpected conditions, incomplete information or improper work distribution, personnel can find themselves unprepared to complete their assigned tasks on a jobsite.
Another factor causing noncompliance errors is that the ways things should be done in theory are not always in sync with the way they are done in practice. Processes and procedures can be inadequate, incomplete, out-of-date, too hard to remember with supporting guidance or otherwise hard to execute.
Oil and gas companies are improving quality, HS&E and bottom-line economic performance by applying digital, collaborative workflow concepts that have proven effective in other industries, combined with consumer-like applications that users intuitively understand how to use.
Noncompliance is sometimes an unintended consequence of inadequate real-time supervision or communication. A field worker who discovers a wrong part when performing maintenance needs to reach an expert immediately. A supervisor and supply chain partner also may need to be part of the conversation. Without collaboration, there is either nonproductive time or noncompliance. Engineers, suppliers and operations need informed consent to make sound real-time decisions.
Errors are not limited to workers in the field. Executives, engineers and supervisors, to name a few, also are susceptible to procedural errors. Simply put, everyone at every level of management is at risk. One deviation can lead to significant consequences through the “Swiss cheese model” or “cumulative act effect,” where active and latent individual errors can combine to cause a major incident.
A Team Sport
Workflows in most oil and gas operations are a team sport, yet there are no widely used collaboration tools that help all team members oversee and participate in decision making and ensure adherence to properly defined procedures. Oversight requires a physical presence, and it can be difficult to completely verify work done without being present at all times. If an expert is required, that expert has historically had to travel to the work site. As a result, little of what happens in the field is typically known beyond an individual or small group present on location and doing the work.
Fortunately, the technology barriers to remote communications have fallen with the ability to connect in real time across standard Wi-Fi and cellular networks. The cost of quality devices to deploy to field workers has also plummeted. When standard communications are not available, new Bluetooth mesh networks can take their place. These networks of beacons and devices enable everyone on a site to communicate with one another.
Usability barriers also have fallen with the reality that every worker now has a mobile device close at hand. Business applications are increasingly designed for the 99 percent who do not work in information technology, and their intuitive user interfaces make it easy to on-board everyone in a company or project team. Collaboration tools for work built with this approach require little or no training as they mirror how the applications they use in their personal lives work.
Collaboration tools bring a new level of productivity and transparency wherever deployed within the oil and gas industry. Team members and managers will be able to watch in real time as work is completed. Operators will be able to coordinate in real time with service companies on the status of parts, components or service delivery. When questions arise at any point, team members will be able to immediately seek assistance from others.
Even the most complex decisions and processes can be broken into a series of documented steps. Only at this micro level is there a chance to standardize outcomes. This is as true for an executive-level decision as it is for a routine maintenance task.
Procedures are commonly used to document repeatable tasks. They are supposed to impose consistency, quality, safety and efficiency. Procedures need to be understood by all, used by only those qualified and authorized, and always accurate and complete to achieve compliance. The gap that has developed between theory and practice can be closed with a digital and measurable approach.
Procedures are usually authored in text form using a word processor or similar tool. File names and storage locations are used to track updated versions, but often there is no automatic control system. Documents are distributed as paper or its proxy, a pdf file.
Consider how much better procedures become when freed from paper bonds. Authors can immediately update procedures and add text, images, video or other rich media content to improve overall understanding. A pump maintenance procedure on paper can only use words and illustrations to describe the process. There is no way to show how the steps were done in the past or hear how the pump should sound, or to ask an expert for assistance. When procedures are digital and supported by collaboration, all these and more become possible. The entire context for procedures moves from static to dynamic, where revisions happen and are deployed quickly.
Paper-based processes also have limited control mechanisms. There is no way to require data entry for a particular step or to validate the number entered. Workers can choose to jump ahead rather than stepping through the procedure. No tangible evidence such as photos and videos can be consistently collected to show that equipment was assembled correctly or that inspections were properly completed. With digital procedures, rules can be built in to ensure that every step is followed and that evidence is collected and experts are available. Even the location can be automatically verified through GPS.
Paradoxically, digital procedures are more easily controlled than those on paper. Manual systems designed to track revisions are cumbersome and at best, difficult to keep current. Costs are incurred with each publication, discouraging rapid and frequent updates. Distribution is difficult to track and it is all but impossible to be sure that the proper version is used. In contrast, digital version control is automatic. In essence, there is too much inertia required to properly distribute and maintain procedures over time.
Everyone knows how to use paper, but they also know how to use smart devices. It is human nature at this point that people are far more likely to carry and refer to a digital device than any paper-based instruction. Digital procedures presented on these devices leverage the familiarity most workers now have with similar consumer applications. Everyone knows how to fill in a form, submit a search query, play a video and take a photo. Virtually no training is required.
Leveraging Feedback
Processes improve with feedback. Arguably the most compelling advance made by taking processes digital is the ability to capture, distribute and leverage feedback for process improvement. There is so much knowledge that can be captured around more effective, safe and efficient ways to complete work.
How many parents have tried to assemble a bicycle or swing set following paper instructions that were poorly written and contained illustrations that hardly resembled the parts in the box? The same thing can happen in the oil field. And in neither case does feedback typically flow back to the procedure authors, nor are there any mechanisms to hold procedure authors accountable for the quality of their instruction. The next person to follow the procedure will face the same unfamiliar words, insufficient illustrations, improper tool list, and so on. Continuous improvement depends on instant and effective feedback from the field. Once this feedback is captured digitally, it becomes transparent, thus creating a means for accountability for the procedure authors.
Exceptions also are poorly handled in a paper-based environment. Deviations, even when appropriate and approved, can spell disaster if not documented. Follow-on decisions even within the same team may be uninformed. Exceptions are necessary in complex environments, but so is transparency. Paper methods do not provide this needed insight and transparency.
For example, if drilling conditions make it necessary to change cement cure time, the changes should be recorded and all involved should have visibility to that decision. Procedures must support this type of dynamic change with the proper authorization and team transparency. Otherwise, every action after this change may be compromised.
There is tremendous power in making the connection between how things should be done in theory and how they actually are done in practice. Enabling everyone to be active participants in process improvement provides great insight into new, better, and safer ways of executing work and brings the team into better alignment.
A digital, collaborative environment is as valuable for executing daily tasks as it is for making multimillion-dollar decisions on a drilling or well completion program. It supports the standardization and transparency needed to avoid errors that lead to the Swiss cheese model of disaster. Every company of every size can benefit.
All it takes to get started is a commitment to digitization and collaboration. Companies should start by defining a project that includes specific assets under management and a diverse team responsible for them. Include a wide group of people across all disciplines and departments in the project definition phase, from senior leadership to drilling supervisors, completions and production operations managers, and field-level technicians to truly demonstrate the power of this approach.
Set goals such as improving safety or reducing nonproductive time improvement. Determine how to measure change and establish metrics to track it. Be sure to understand and measure user satisfaction, since this is a critical element of success. If people cannot easily do their jobs for whatever reason, the project likely will fail.
By starting with a small, well-defined project, results should be evident within only a few weeks. Improvement will be easy to measure: work done in the field matches procedures as written. If not, procedures may need to be redesigned or field work may need to be examined to find the reason for any discrepancies, which can now happen in real time.
Leading companies already are seeing reductions in noncompliance as well as nonproductive time. By applying concepts that have worked well in other industries, combined with consumer-like applications users already know how to use, oil and gas companies can make serious advances in quality, safety and bottom-line economic performance.
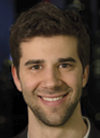
Chase Feiger is the founder and advisor for strategic partnerships at Parsable. Feiger previously served as an associate at First Round Capital, as founder and chief operating officer of Dyad.com, and as a strategy consultant at Accenture. He holds a bachelor’s from the University of Pennsylvania, a master’s in operations management and finance from the University of Cambridge, and a doctor of medicine from the Icahn School of Medicine at Mount Sinai.
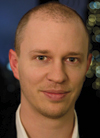
Ryan Junee is the founder and president of Parsable. He previously started several companies, one of which was purchased by Google, and he mentors other startups through prestigious Silicon Valley institutions such as Y-Combinator. He dropped out of the Ph.D. program in electrical engineering at Stanford University to pursue his passion for high-technology startups. He holds a master’s in electrical engineering from Stanford, as well as bachelor’s degrees in computer engineering, finance and commercial law from the University of Sydney.
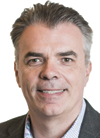
Lawrence Whittle is the chief revenue officer of Parsable. He has spent the past two decades successfully building enterprise software companies on a global scale. Whittle has held customer success, sales, marketing and general management leadership positions in companies in both North America and Europe. He has a specific passion for software that transforms the operational effectiveness of industrial companies. Whittle holds a degree in business and accounting from the University of East London.
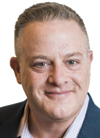
Ken Pulverman is the chief marketing officer of Parsable. He led marketing for four previous startups, one of which conducted an IPO and another of which was acquired at a premium. Prior to this, Pulverman led product marketing for CRM at Oracle. He started his career in software working in alliances, solution marketing and product management at Siebel Systems, and in express logistics for Stanford University, DHL and TNT Express Worldwide. He holds a bachelor’s in international relations from the University of California Davis and an M.B.A. from the University of Michigan.
For other great articles about exploration, drilling, completions and production, subscribe to The American Oil & Gas Reporter and bookmark www.aogr.com.