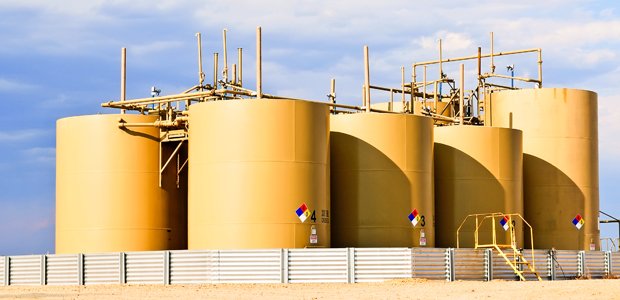
Vapor Recovery
Study Gathers Data on Oil Tank Vapor Pressures
By Mark Goloby
HOUSTON–Fugitive vapors from crude oil production tanks are becoming a bigger regulatory issue in virtually every state. These vapors are Btu-rich and have financial value if recovered and added to the sales stream.
The challenge for oil and gas operators is recovering tank vapors in a cost-effective manner. By integrating the right technological components, the industry can economically capture and monetize tank vapors with a low-power, low-volume, and low-cost recovery solution. Producers can meet regulatory compliance and achieve a return on their investment in a compliance system, or at least offset some of the costs.
One study is gathering tank vapor pressure data using a solution that combines the Internet of Things (IoT) with low-pressure monitoring devices (less than 1.0 psi). Various deployments have been undertaken primarily to test the sensitivity of the devices and gather, monitor and measure tank pressures in a variety of production tank configurations.
Redbud Exploration & Production is conducting raw research and data collection of tank battery installations of the low-cost system to gather pressure readings and document the effects of:
- Ambient temperatures;
- Fluid levels within the tank;
- Air space pressure between the fluid level and the top of the tank;
- Fluid temperature; and
- Production process equipment influence on tank pressures, including separators, heater treaters and dehumidifiers.
There are practical and beneficial aspects of performing these studies. In one study, it was determined that seals and springs on the tank’s thief hatches may not have been performing at the specified pressure containment level. Methane detection equipment was brought to the tank site to monitor emissions around the seals, which indeed confirmed that methane was leaking around the hatches. The results not only validated the measurements, but the information assisted the client in identifying changes to consider in replacing seals and springs.
Gathering pressure measurements has several goals and objectives. The fundamental drive is to develop a procedure to evaluate a tank battery to be outfitted with a vapor recovery unit. The installation of a cost-effective VRU is part of an ongoing goal to capture escaping fugitive emissions from production tanks to both monetize the gaseous vapors as well as achieve environmental regulatory compliance.
At this point, the effort is essentially basic research, starting with rudimentary data gathering of in situ tank battery installations. There are several challenges to gathering this information, including the age and condition of oil tanks, and the condition of hatch seals, relief valves, vent springs, and vapor pressure relief configuration.
Low Pressures
Underlying all of this are the relatively low pressures involved. Basically, tank pressures are measured in ounces of pressure or inches of water column in which 1.0 psi of pressure is equal to 27.708 inches of water column. Although the pressure is low, in a volumetric sense, 0.5 psi (eight ounces) of pressure can blow a person’s hat off upon opening the hatch. A typical field production tank is built to withstand an internal pressure of 16-24 ounces of pressure per square inch.
The technology being tested on Redbud Exploration & Production’s tanks uses an IoT device to measure the extremely low ounces of psi. This provides constant monitoring of the pressures with notification levels set to capture events, and enables regular reporting intervals (the system is usually set to capture data on an hourly basis). However, when the application calls for it, data can be gathered in smaller time increments for tighter analysis. Instances where this may be desired are field configuration changes, trial runs of a VRU, or occasionally, to verify VRU performance, efficiency and operation.
Because it is an IoT-based solution, building the database is fairly straightforward and easy. The trick is to then analyze the data and correlate the instrument measurements to actual field events and activity. On one occasion, a disruption in field production sent volumes from one tank battery to another. This push of fluid increased the pressure in the receiving tank battery. The instruments successfully detected, measured and reported the incident, which was corroborated by field operating personnel.
Some of the early data collected revealed the relationship between pressure relief and compromised tank seals. Other findings include how changes in ambient temperature impact tank pressure, but the fluid temperature is more significant. Fluid temperatures influence internal pressure much like hot water in a pressure cooker. The separation of gas, oil and water is critical to most production facilities. Because they unload during separation, these devices can send bursts of pressure into the production tanks that can raise pressures quite high for an instant.
It is also desirable to understand pressure dynamics as the tank fluid level rises to the top of the tank. A VRU designed to commence compression based on head pressure requires more understanding of how rising fluid levels build pressure in the shrinking air gap space. How quickly pressures build and need to be relieved by the VRU can determine how many times the VRU will activate.
To design a low-cost and efficient system to reduce fugitive emissions and monetize them, the current scale and scope is to broaden the database through continual data accumulation on as many different field tank configurations and situations as possible. The next step in the study is correlating facility configurations, operating dynamics and vapor pressure characteristics for better design and vapor pressure management for fugitive gas capture.
Editor’s Note: The author acknowledges the assistance of William Shelton, P.E., in developing this article.
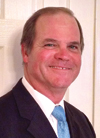
MARK V. GOLOBY is president of Houston-based TC Technologies, which is involved in a variety of initiatives to deliver wireless monitoring tools for oil and gas production, and the assets needed to support that production. Goloby has more than two decades of experience in implementing cost-effective wireless data solutions. He was previously with Mertrix Networks and is a graduate of Texas A&M University.
For other great articles about exploration, drilling, completions and production, subscribe to The American Oil & Gas Reporter and bookmark www.aogr.com.