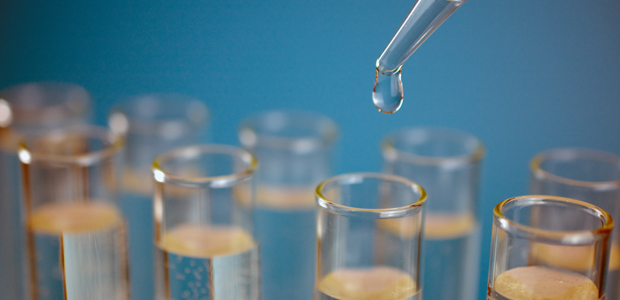
Water Treatment
Technologies Advance Produced Water Treatment, Reuse
By Erica Folio Dintaman, Olayinka Ogunsola, Elena Melchert and Evan Frye
WASHINGTON–Recycled produced water can be a valuable resource for drilling and fracturing operations in unconventional oil and gas plays, as well as other beneficial uses. However, the major barrier to recycling produced and flowback water is the high cost associated with treatment. The characteristics of these waters can vary greatly, requiring an array of treatment technologies for different treatment targets in different oil and gas basins.
The U.S. Department of Energy conducts early-stage research as part of its produced water management R&D portfolio with the goal of developing and advancing technologies and tools to improve produced water treatment and management. As part of this ongoing work, DOE-funded projects have investigated and developed several advanced technologies that include all three primary areas of produced water treatment: “clarification” (removing oil and grease, solids, salt, microbiological organisms and other contaminants), “softening” (reducing ions that cause hardness) and “desalinating” (reducing chlorides).
The objective is to develop technologies that can reduce the cost of treatment to safely recycle/reuse produced water. This will decrease the industry’s reliance on freshwater and reduce well production costs in unconventional plays, which in turn, will enable greater development of the nation’s unconventional hydrocarbon resources. Some additional tangential benefits can also be derived, including reducing the quantity of water that must be disposed of via deep well injection.
The insights gleaned from these projects not only increase the field-readiness of promising treatment processes, but also advance the industry’s state of knowledge to help overcome common challenges, including reducing cost, increasing mobility and flexibility (for varying quantities and contaminants), and optimizing efficiency and durability of produced water treatment methods. Specific resulting advancements include:
- Antifouling membranes that remove organic material and bacteria with less sensitivity to water variability;
- Technologies to treat water with high barium (Ba) and radium (Ra) concentrations; and
- A prototype forward osmosis desalination system with 90% salt rejection capability.
Clarifying Technologies
Some of the clarification technologies investigated as part of DOE-funded research include forward osmosis (FO), humidification-dehumidification, plasma, magnetic ballast clarification (MBC), crystallization, and nanofiltration (NF)/ultrafiltration (UF) membranes. Because onsite produced water treatment systems are typically only needed in unconventional plays during post- fracturing flowback, all of the research is noticeably focused on mobile pretreatment processes and systems.
An example of this is an onsite multimedia filtration system developed at West Virginia University that efficiently treats flowback water at varying conditions over time (Figure 1). The mobile treatment unit (MTU) consists of two filtration units. During field testing in the Marcellus Shale, a prototype MTU removed 32% of suspended solids, processed 280,000 gallons of produced water (98.6% of which was recycled for fracturing operations), and removed particles as small as 0.5 microns. The system excelled at responding to variable water quality, but test results suggest a module should be added to the front end of the MTU to decrease oil content to prevent oil/polymer from slowing throughput.
In response to the common challenge of membrane fouling, developing more durable filtration membranes has been a thrust of the research. A study by Southern Research Institute (SRI) demonstrated a novel antifouling option for treating water for reuse in hydraulic fracturing: a vortex-generating filtration membrane. The system can be fitted to a range of membrane types for high-fouling wastewaters with high solids content. It prevents suspended solids from collecting on a membrane’s surface by employing rotating, vortex-generating blades above the membrane’s surface.
SRI researchers also evaluated the use of MBC alone and in conjunction with the vortex-generating membrane system. MBC uses coagulation and flocculation processes, with the addition of magnetite, to generate and remove a magnetic floc. It is suitable for removing suspended solids and iron, and its smaller footprint makes it portable. The MBC process alone showed success in producing common reuse criteria in eight of nine demonstrations, and reduced total suspended solids (TSS) to below limits for reuse in 88% of demonstrations. In additional tests, MBC was enhanced by pre-oxidation to remove (precipitate) dissolved iron.
Several projects have tested novel and innovative processes for clarifying produced water. An example is highly absorbent and organophilic swellable glass material developed by ABS Materials Inc. Testing of mobile pilot systems demonstrated that this material could remove >99% of dissolved benzene, toluene, ethylbenzene and xylene (BTEX), as well as 50% of ionic surfactants at a treatment rate of 60 gallons/minute. This swellable glass material also was one of the subjects of a complementary project conducted by Texas A&M University to field test pretreatment options, which again demonstrated this medium’s ability to decrease oil and grease levels.
Another innovative process for organic removal is an integrated plasma filtration system that uses high-voltage discharges to address multiple targets simultaneously. The system was developed by Drexel University and includes plasma-induced water softening, advanced filtration, and a mechanical vapor compression (MVC) distillation system. The advanced filter utilizes the shock waves from spark-type plasma discharges to allow stainless steel cartridge filters to self-clean. In addition to removing hydrocarbons such as BTEX, polycyclic aromatic hydrocarbons (PAH), and alkylphenols, plasma arc discharge treatment successfully disinfected and oxidized (reduced bacteria) at higher flow rates.
Finally, DOE-sponsored research at Clemson University developed and tested the effectiveness of a constructed wetland produced water treatment system. This research showed that constructed wetland systems can be targeted to treat specific constituents commonly found in produced waters (metals, metalloids, oil and grease, ammonia, etc.). Four waters were treated with individually developed pilot-scale systems that allowed for tailored “biogeochemical” conditions and a particular treatment sequence to remove specific constituents.
Softening Technologies
Softening produced water involves removing or reducing the presence of divalent cations, primarily “hardness ions” such as calcium (Ca), magnesium (Mg) and strontium (Sr), which can react to form membrane-fouling scale. However, other constituents found as divalent ions in produced water–namely Ba and Ra–also can be removed by softening procedures.
Researchers at GE Global Research conducted laboratory testing and cost analysis of two promising processes for treating waters with high Ba concentration and Ra activity. One technique uses a modified lime-soda softening process to initially remove Ca, Mg and Sr (for disposal as a nonhazardous waste), followed by precipitation of Ba and Ra as carbonates. The precipitated Ba and Ra carbonates are re-dissolved to yield a liquid concentrate for underground wastewater injection. The second process uses manganese dioxide (MnO2) adsorption to remove Ba and Ra in a liquid concentrate.
If the produced water is subsequently treated with a thermal crystallizer, both processes can reduce Ba and Ra concentrations in the salt product to below the required limits for reuse as road salt. While the estimated cost for the second process is lower, it would be more difficult to scale up and requires additional research to establish feasibility.
A related effort validated a sulfate pretreatment process for removing Ba and Ra. Sulfate treatment was shown to produce a solid solution of Ba and Ra sulfate, in this case, at a level below what is considered hazardous solid waste. Therefore, the sulfate sludge can be cost-effectively disposed of as a nonhazardous waste. It is used in combination with a lime/sodium hydroxide (NaOH) pretreatment process to remove iron and manganese. This enables the produced water to be further treated for salt recovery.
UF and NF membranes also can be used to soften produced water, but it is challenging to maintain membrane performance in operating situations with high temperatures, frequent system upsets or stops for cleaning, and where organic solvents and oxidizers are used. In addition to SRI’s vortex-generating NF and UF membrane with antifouling capability, University of Southern California researchers studied ceramic UF and NF membranes. When preceded by chemical precipitation treatment, the process removes 98% of hardness-contributing cations. While performing slightly worse than polymeric membranes, ceramic membranes are expected to have longer lifetimes and to be easier to clean.
In the Drexel University project, plasma arc discharges were used to dissociate and remove bicarbonate ions to reduce the “temporary hardness” caused by the presence of Ca and magnesium bicarbonate. This, in turn, helps to prevent fouling from calcium carbonate scale. The research determined that removing bicarbonate is a more prudent strategy for preventing fouling in produced waters where calcium ions are more abundant than bicarbonate ions.
Desalination Technologies
Produced water is typically highly saline, making salt reduction critical to reuse. DOE has conducted a breadth of research projects aimed at improving both membrane and thermal desalination processes.
Membrane-based projects have sought to extend the application of FO, reverse osmosis (RO), and NF/UF membranes to treating total dissolved solids in produced water. A comprehensive study by GTI applied electrodialysis, RO, and NF/UF membranes to desalinate water produced from the Marcellus and Barnett shales. The analysis provides recommendations to improve the economic feasibility of the electrodialysis process, such as iron pretreatment.
Since the major challenge with desalination membranes is fouling, an effective antifouling polydopamine (PDOPA) surface coating was developed as part of the GTI research. PDOPA improved the performance of RO, NF and UF membranes in laboratory testing, showing increased flux. This also was demonstrated in a field test of UF and RO membranes conducted by GTI at a water reclamation facility in the Barnett (Figure 2). In this test, the coated membranes increased salt rejection under high-salinity conditions (RO) and increased flux (UF).
A project at the Colorado School of Mines investigated osmotically driven membrane processes such as FO and UF membranes, including studying the impact of produced water exposure on the membranes and evaluating environmental and economic impacts of FO systems. This analysis provided wide-ranging insights into the specifications that result in the most effective FO membrane (for example, membrane chemistry that tolerates large shifts in pH). Future development could lead to osmotic membrane processes with better rejection, water flux and operating efficiency. A related project pilot tested a prototype desalination system that reduces the risk of membrane fouling using a system of paddles that clean and protect the membrane surface.
With DOE support, Eltron R&D Inc. has developed NF membranes that better handle high temperatures, exposure to organic solvents, wear and aging. These membranes have demonstrated the ability to reduce more than 60% of magnesium sulfate, and applicability to separating NaCl (~20-26%) under certain conditions. Many additional avenues of research were identified in this project, including studying chemical cleaning of FO membranes and environmental and economic impacts of FO membranes in different oil and gas basins.
In regard to thermal processing, research by Altela Inc. tested a thermal distillation technology to separate pure water from brackish produced water in the Marcellus. The system is powered by natural gas, which reduces the cost relative to electricity. Improvements from this project demonstrated a 45% increase in overall energy efficiency compared with earlier models of the same technology. Indications are that the technology can be successfully deployed in the Appalachian Basin to cost-effectively treat and reuse flowback water as opposed to trucking and disposal.
Researchers at the New Mexico Institute of Mining & Technology demonstrated a passive solar-powered humidification-dehumidification (HDH) desalination process. An earlier DOE-supported project designed the HDH process, which under lab conditions removed 99.5% of dissolved salts and handled varying total dissolved solids levels. In a subsequent field test in Eddy County, N.M., the system used the solar panels to power the desalination of produced water. The results showed an annualized average of nine bbl/d of freshwater from an average of 20 bbl/d of produced water, although the system’s performance varies with humidity and air temperature.
After developing the sulfate pretreatment process for Ba/Ra removal, GE Global Research developed a membrane distillation system driven by mechanical vapor compression (MVC-MD) to desalinate pretreated produced water. This evaporation process concentrates and reduces brine volume so it can be more easily handled. As part of the technology’s pilot testing, the MVC-MD produced a high-quality distillate and operated with less than 10% downtime in a seven-day test in the Barnett Shale.
Full System Processes
Some projects have taken a “full systems approach” to designing an entire process to meet a specific produced water need. For example, researchers at Texas A&M addressed the treatment needs of high-salinity brine (>100,000 TDS) by developing a mobile, multifunctional treatment process that removes all hydrocarbons, suspended solids and bacteria. The researchers combined and tested two filters that remove oil and grease, one system that uses a modified naturally occurring material filter to remove BTEX, and three microfilters that remove solids. These clarifying processes were combined with nanofiltration in a lightweight, trailer-based mobile unit.
In general, multiple field tests showed the treatment options are capable of treating high-salinity waters without fouling, although key challenges noted included high iron content and high bacterial counts.
A related effort by New Mexico Institute of Mining & Technology developed a two-stage solution that uses a portable antifouling hollow fiber membrane (HFM) filtration process. In the first step, BTEX is removed using HFMs with a tailored morphology and preparation to prevent fouling. In the second stage, a second type of HFM is used for desalination. A field test of this system showed the ability to treat 10-12 bbl/d with a clean water recovery of approximately 60%.
GE Global Research has developed a process to treat water with relatively low TDS (~<45,000 parts per million) by designing systems for four purification levels: clarified only for reuse; clarified and softened for reuse; clarified, softened and desalinated for reuse; and clarified, softened and desalinated for discharge. Through bench-scale analysis of existing technologies and process formulation, it was concluded that “membrane systems, in combination with appropriate pretreatment technologies, can provide cost-effective recovery of low-TDS flowback water for either beneficial reuse or safe surface discharge.”
A project conducted by Ohio University looked at the “integrated precipitative supercritical (IPSC)” process, which combines technologies such as filtration, ultraviolet light treatment and chemical precipitation using an advanced supercritical reactor. The entire developed process combines commercially available technologies for precipitation of target dissolved species and NORM removal, with TDS removal via supercritical water treatment, and supercritical water oxidation of hydrocarbons.
Finally, a process developed by the University of Wyoming demonstrated a technology that transforms traditional drip irrigation equipment into an integrated water treatment and reuse process. It uses a pervaporation membrane as the drip tape to deliver irrigation water to plants, providing drops of water over time. In a field trial, the water was desalinated through a pervaporation membrane and used to irrigate alfalfa in Wyoming. Although successful, pervaporation treatment volume is limited and cost-challenged compared to other treatment alternatives.
While all of these projects have shown promise, many of these diverse technologies are still progressing and more research is necessary to validate lab and field test results, investigate cost-effectiveness, and ensure field-readiness in unconventional plays. Even so, DOE’s research portfolio has collectively advanced the understanding of produced water treatment options, and the results can help operators identify options to responsibly manage their produced waters.
As these and other projects illustrate, the development and use of advanced treatment technologies can help produced water become a revenue stream to improve overall well economics to further promote the development of domestic resource plays.
Editor’s Note: On May 13, U.S. DOE’s Office of Fossil Energy announced up to $5 million in federal funding for cost-shared R&D projects under the funding opportunity announcement (FOA) DE-FOA-0002004, Low Cost, Efficient Treatment Technologies for Produced Water. The National Energy Technology Laboratory will manage the selected projects, which will focus on developing new technologies and improving the efficiency of existing commercial processes, specifically, those that target removing challenging constituents from produced waters.
DOE says it anticipates selecting up to four projects for this FOA. For more information visit the opportunity summary page or the Office of Fossil Energy website.
ERICA FOLIO DINTAMAN is a special assistant at the National Oceanic & Atmospheric Administration. Before joining NOAA last year, she was a general engineer in the upstream research division of the U.S. Department of Energy’s Office of Fossil Energy’s Office of Oil & Natural Gas. Folio Dintaman holds a B.S. in geosciences from Penn State University and an M.S. in engineering management from George Washington University.
OLAYINKA OGUNSOLA is senior program manager in DOE’s Office of Oil & Natural Gas. Dr. Ogunsola has more than 40 years of experience in research and development in the areas of fuel and energy science and engineering, and oil and gas program management, policy and strategy development, and planning.
ELENA MELCHERT is a petroleum engineer and the director of the Upstream Oil & Gas Research Division in DOE’s Office of Fossil Energy. She joined DOE in 1985, and has extensive experience in upstream oil and gas field operations, research and development, policy development, project management, program management, technology transfer, strategic planning and budget development.
EVAN FRYE is an energy industry analyst in DOE’s Office of Oil & Natural Gas. He joined DOE in 2014 after serving as an economist at the Department of Agriculture and a geologist at the U.S. Energy Information Administration. Frye holds a B.A. in environmental science/geosciences from Franklin & Marshall College, an M.S. in energy and mineral engineering from Penn State University, and an M.B.A. from Johns Hopkins University.
For other great articles about exploration, drilling, completions and production, subscribe to The American Oil & Gas Reporter and bookmark www.aogr.com.